www.industrymiddleeast.com
18
'08
Written on Modified on
iQ+
The new iQ+ electronic monitoring and control system, developed specifically by Gravograph for its range of engraving machines, increases their speed by up to 50%. iQ+ also enables new functions to be provided, including secure control of additional accessories, the “Point n’Shoot” positioning aid and automatic integration of the latest Gravograph innovation for producing Braille in signage. iQ+ is fitted as standard to Gravograph’s M and IS series machines manufactured since March 2009.
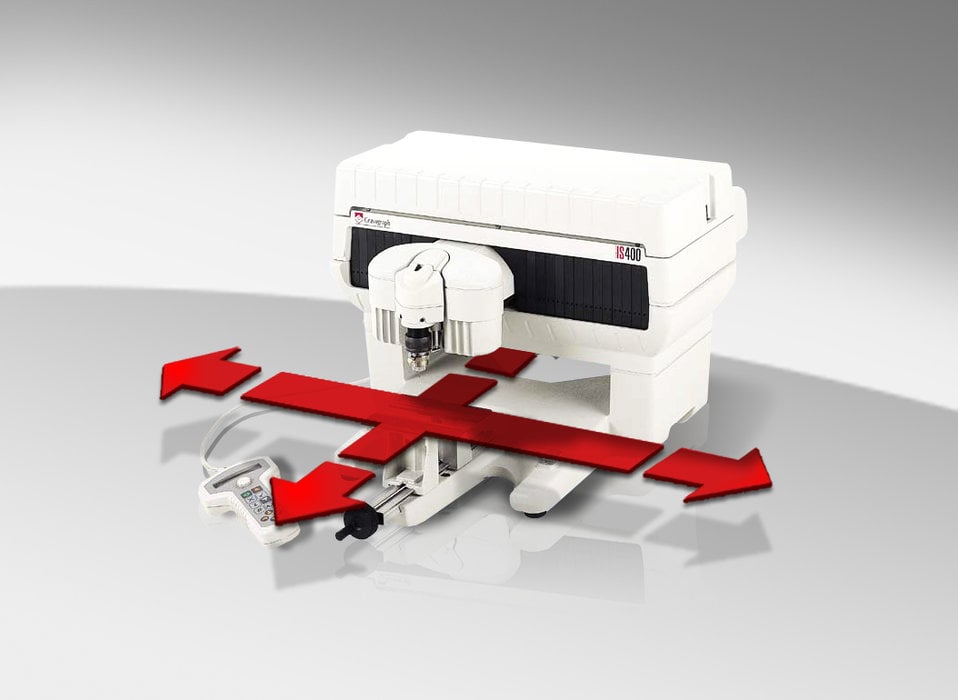
While R&D efforts in recent years have focused on marking quality, the latest line of research of the GRAVOGRAPH teams has been to redevelop the programming of the electronic controls of the machines in order to increase their working speed by 10 to 50% while maintaining the high marking quality level.
In practice, three types of movement have been optimized. First, the vertical movement speed of the spindle in the Z-stroke. In an engraving job there are a very large number of ‘pen up’/‘pen down’ movements which account for a substantial part of the cycle time. With the iQ+ control and command electronics this speed increases, for example from 25 to 40 mm/s on the M20/M40 models and from 35 to 120 mm/s on IS400 and IS1000. Next, the off-load speed, to optimize movements when the spindle is in the raised position, between two engraving passes. This parameter has a strong influence on the overall job completion time. These speeds increase from 25 to 50 mm/s on an M20 and from 60 to 150 mm/s on an IS400. Lastly, the diamond scoring speed, when the work consists in engraving with a non-rotating diamond on an anodized aluminium plate, for example. This offers the customer the option of completing the work more quickly, as this marking procedure does not have the limits of cutters with generation of swarf.
iQ+ also enables many new functions to be provided, such as automatic offset for Gravograph’s BRAILLE SYSTEM, used to mark Braille text. The electronics can now automatically control the offset between the drilling spindle and the bead insertion system that generates the raised Braille text. iQ+ is also the basis for Point n´Shoot and remote control. The Point n´Shoot function provides a laser pointer to position the engraving visually on the object and simulate the engraving work before the job to be completed is actually carried out. The remote control function controls the machine and manages the engraving parameters once the information about the job to be completed has been transferred to the machine electronics. The machine then operates autonomously. The job storage capacity of the Gravograph machine electronics has been multiplied by 4 with the new CPU boards. All the IS machines, for example, now have 32 Mbytes of memory capacity. Jobs such as DataMatrix marking or logos with a large number of vectors can be transferred in a single operation, without risk of information loss.
The iQ+ electronics also extend the marking capabilities of the machines. A long item, normally too large for the machine, can be marked in several runs. The machine informs the operator when the support has to be shifted or repositioned.
To provide higher safety levels for the operators, iQ+ also features fully integrated management of accessories, such as automatic startup and shutdown of external attachments. An example is the integration of High Frequency spindles: the iQ+ electronics can start and stop the spindle automatically with the machine, and spindle rotation is now controlled directly by the machine remote control. iQ+ also provides secure control of approach speeds on XP tables, developed in collaboration with standardization bodies.
Gravograph technicians can easily upgrade previous-generation machines to iQ+ standard.
Photo captions:
-IS400.jpeg: iQ+ extends the marking capabilities of the machines
-logo_IQ.jpeg: The iQ+ logo
-pointandshoot.jpeg: iQ+ is the basis for the Point n´Shoot positioning laser pointer
In practice, three types of movement have been optimized. First, the vertical movement speed of the spindle in the Z-stroke. In an engraving job there are a very large number of ‘pen up’/‘pen down’ movements which account for a substantial part of the cycle time. With the iQ+ control and command electronics this speed increases, for example from 25 to 40 mm/s on the M20/M40 models and from 35 to 120 mm/s on IS400 and IS1000. Next, the off-load speed, to optimize movements when the spindle is in the raised position, between two engraving passes. This parameter has a strong influence on the overall job completion time. These speeds increase from 25 to 50 mm/s on an M20 and from 60 to 150 mm/s on an IS400. Lastly, the diamond scoring speed, when the work consists in engraving with a non-rotating diamond on an anodized aluminium plate, for example. This offers the customer the option of completing the work more quickly, as this marking procedure does not have the limits of cutters with generation of swarf.
iQ+ also enables many new functions to be provided, such as automatic offset for Gravograph’s BRAILLE SYSTEM, used to mark Braille text. The electronics can now automatically control the offset between the drilling spindle and the bead insertion system that generates the raised Braille text. iQ+ is also the basis for Point n´Shoot and remote control. The Point n´Shoot function provides a laser pointer to position the engraving visually on the object and simulate the engraving work before the job to be completed is actually carried out. The remote control function controls the machine and manages the engraving parameters once the information about the job to be completed has been transferred to the machine electronics. The machine then operates autonomously. The job storage capacity of the Gravograph machine electronics has been multiplied by 4 with the new CPU boards. All the IS machines, for example, now have 32 Mbytes of memory capacity. Jobs such as DataMatrix marking or logos with a large number of vectors can be transferred in a single operation, without risk of information loss.
The iQ+ electronics also extend the marking capabilities of the machines. A long item, normally too large for the machine, can be marked in several runs. The machine informs the operator when the support has to be shifted or repositioned.
To provide higher safety levels for the operators, iQ+ also features fully integrated management of accessories, such as automatic startup and shutdown of external attachments. An example is the integration of High Frequency spindles: the iQ+ electronics can start and stop the spindle automatically with the machine, and spindle rotation is now controlled directly by the machine remote control. iQ+ also provides secure control of approach speeds on XP tables, developed in collaboration with standardization bodies.
Gravograph technicians can easily upgrade previous-generation machines to iQ+ standard.
Photo captions:
-IS400.jpeg: iQ+ extends the marking capabilities of the machines
-logo_IQ.jpeg: The iQ+ logo
-pointandshoot.jpeg: iQ+ is the basis for the Point n´Shoot positioning laser pointer