www.industrymiddleeast.com
20
'09
Written on Modified on
Leading car manufacturer Renault solves unwanted engine noise and vibration using Maple
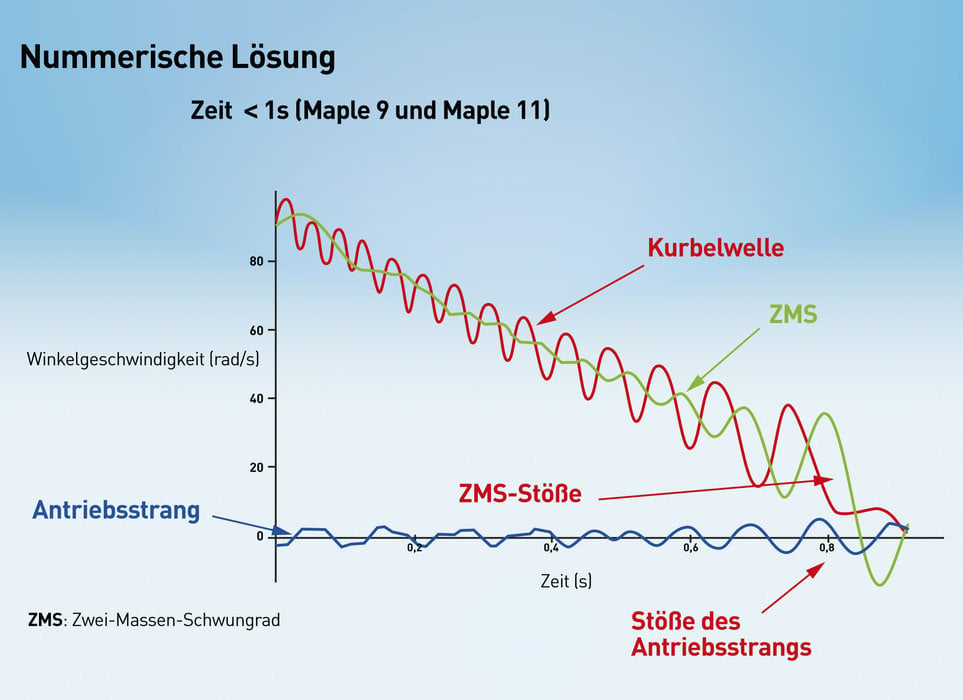
When an engine stops, several engine components take part in the process. Components can produce unwanted noise and vibrations when the engine slows down, which can lead to their deterioration. Jean-Louis Ligier, a Research and Development manager at Renault, and his team were tasked with determining the sources of these noises and vibrations in a 2.2 liter 4-cylinder turbo diesel engine. They found Maple™ to be the most efficient tool to model the engine and determine the source of the unwanted noise. More importantly, they also used Maple to determine a solution to the problem.
Ligier, who has a Ph.D. in Mechanical Engineering, has been using Maple for over 20 years. He has used the software in several applied research projects, such as time-varying thermal analysis in gearbox components, engine friction optimization, and vibration analysis. He has been with Renault for over 12 years, managing thermal behaviors and mechanic fatigue on engine components, as well as determining new simulation methodology for them. His primary goal in using Maple was to write equations that control the engine components very easily.
When creating mathematical models of various components, different software can be implemented. Ligier has found through his experiences that Maple is the easiest and fastest software for his tasks. "In comparison with others, Maple can do in a couple of hours what other software can take days to compute," he said. "The natural math notation allows me to enter the equations as if I were writing them by hand. The fact that I can do symbolic calculations allows me to do optimizations that are virtually impossible with other software. What’s more, the results are extremely accurate."
When speed decreases in an engine, several mechanical resonances are generated. If there is too much movement within the engine, not only do the components create noises disturbing to the driver, but they also begin to wear out prematurely. The goal of the study was to model and understand the cause for the vibrations. The modeled engine was a 4-cylinder from Renault’s Laguna line of cars. The model of the engine was a system of five differential equations and focused primarily on the crankshaft, the dual mass flywheel (DMF), as well as the whole power train. From these equations, Ligier could estimate the level of vibration created during the deceleration of the engine. After plotting the results of the simulation, it became apparent that the vibrations were primarily occurring from shocks inside the DMF. To rectify the problem, a rather simple solution was implemented, which involved modifying the air intake while decelerating.
Discovering the exact cause of the problem led to a substantial cost-saving benefit to Renault because it meant that the problem was fixed with a simple solution—only a slight modification of the engine was required.
By analyzing the simulation results, Ligier reduced the noise by as much as 30%. Modeling the engine in Maple allowed him to analyze the symbolic equations, which enabled a more in-depth understanding of the system. The numeric results were plotted and the location of the unwanted vibrations was discovered. By using Maple, he was able to create and run his model in one day, which was a substantial time saver in comparison to other software, which took over a week for the same task. "I have been using Maple for over 20 years. I have always liked how easy it is to use, and how powerful it is. The ability to perform both symbolic and numeric computations is a huge time saver for me, allowing me to get results in a day, instead of weeks with other software," concluded Ligier.
Ligier, who has a Ph.D. in Mechanical Engineering, has been using Maple for over 20 years. He has used the software in several applied research projects, such as time-varying thermal analysis in gearbox components, engine friction optimization, and vibration analysis. He has been with Renault for over 12 years, managing thermal behaviors and mechanic fatigue on engine components, as well as determining new simulation methodology for them. His primary goal in using Maple was to write equations that control the engine components very easily.
When creating mathematical models of various components, different software can be implemented. Ligier has found through his experiences that Maple is the easiest and fastest software for his tasks. "In comparison with others, Maple can do in a couple of hours what other software can take days to compute," he said. "The natural math notation allows me to enter the equations as if I were writing them by hand. The fact that I can do symbolic calculations allows me to do optimizations that are virtually impossible with other software. What’s more, the results are extremely accurate."
When speed decreases in an engine, several mechanical resonances are generated. If there is too much movement within the engine, not only do the components create noises disturbing to the driver, but they also begin to wear out prematurely. The goal of the study was to model and understand the cause for the vibrations. The modeled engine was a 4-cylinder from Renault’s Laguna line of cars. The model of the engine was a system of five differential equations and focused primarily on the crankshaft, the dual mass flywheel (DMF), as well as the whole power train. From these equations, Ligier could estimate the level of vibration created during the deceleration of the engine. After plotting the results of the simulation, it became apparent that the vibrations were primarily occurring from shocks inside the DMF. To rectify the problem, a rather simple solution was implemented, which involved modifying the air intake while decelerating.
Discovering the exact cause of the problem led to a substantial cost-saving benefit to Renault because it meant that the problem was fixed with a simple solution—only a slight modification of the engine was required.
By analyzing the simulation results, Ligier reduced the noise by as much as 30%. Modeling the engine in Maple allowed him to analyze the symbolic equations, which enabled a more in-depth understanding of the system. The numeric results were plotted and the location of the unwanted vibrations was discovered. By using Maple, he was able to create and run his model in one day, which was a substantial time saver in comparison to other software, which took over a week for the same task. "I have been using Maple for over 20 years. I have always liked how easy it is to use, and how powerful it is. The ability to perform both symbolic and numeric computations is a huge time saver for me, allowing me to get results in a day, instead of weeks with other software," concluded Ligier.