www.industrymiddleeast.com
30
'09
Written on Modified on
Improved quality of weld repair of rail defects at reduced costs from Tata Steel
Tata Steel Rail has developed a novel technique for the cost effective repair of discrete defects on the running surface of rail. The key strength of this novel technique lies in the replacement of those aspects of the conventional Manual Metal Arc (MMA) process that often result in variability in the quality of the repair with automatic and more controlled operations. The developed semi-automatic process employs open arc welding with flux cored arc wire and relies on a low preheat temperature to proactively control the metallurgical transformations within the Heat Affected Zone (HAZ). Given that an average cost per repair or short replacement rail can run into several thousands of euros and that the occurrence of wheel rail interface defects is likely to increase with the evident increase in levels of traffic on most railways, the importance of the new process is easy to understand.
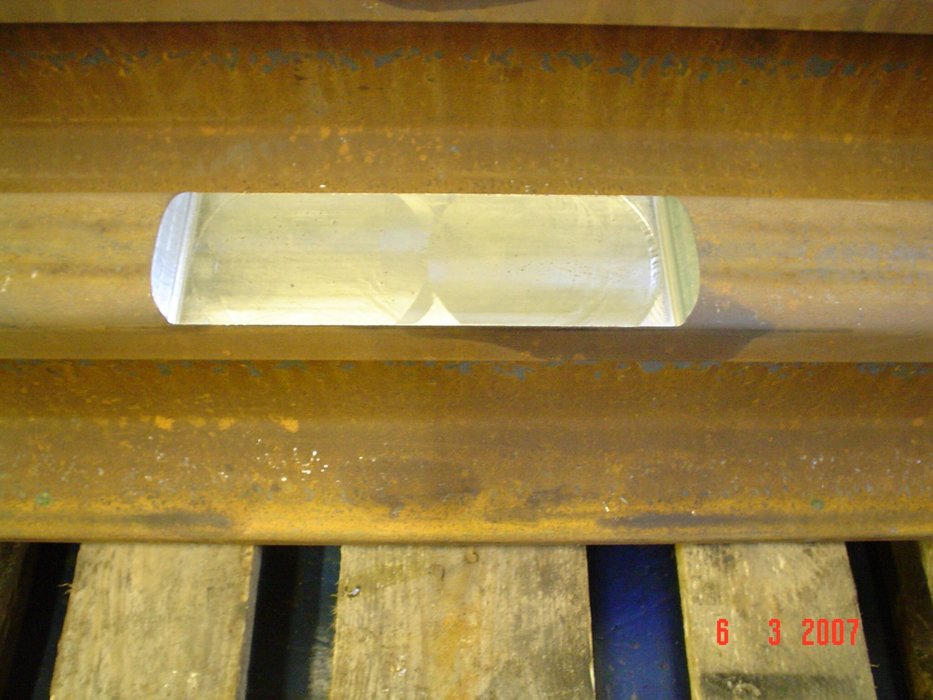
The process has been thoroughly tested and a dedicated unit is currently being manufactured to undertake in-track demonstration in several European networks including France and UK.
The running of carriage wheels on rails creates high and complex stress patterns within the rail/wheel contact patch, leading to surface degradation. The wide range of track design, wheel profiles, and types of traffic can result in a variety of surface defects that reduces the life of the rail. Defects such as squats and wheelburns occur even in the most modern and well maintained railway networks and, as a broad general rule, every network develops one such defect each year, every two kilometres. The replacement of such defects with a short rail section is expensive and not always desirable as it introduces two new discontinuities in the track in the form of two aluminothermic welds (exothermic reaction using aluminium as the reducing agent) that destroy the advantages obtained with long hot-rolled rail (up to 120 metres). The alternative conventional technique for the repair of such defects is the Manual Metal Arc (MMA) welding process. Although the technique is used many industries, it is heavily reliant on the competence of the welder, is time consuming, and is prone to internal defects such as porosity that subsequently grow through fatigue, and if not detected by ultrasonic inspection, result in rail breaks.
The following factors contribute to the cost effectiveness and technical robustness of the new developed process:
1.The move away from the conventional preheating temperature of 350°C to just 80°C has the advantage of faster repair, reduced depth of heat affected zone, and more robust microstructure.
2.The use of a standardized removal of the defect area by controlled milling has the advantage of reproducibility and removes the subjective judgement of the operator.
3.The use of a semi-automatic programmed open arc welding process with flux cored arc wire ensures control of heat input and predictable operational times.
The quality of the weld restored running surface from the developed process is ensured as the repair is extremely resistant to fatigue and has similar wear resistance to that of the standard Grade R260 rail with uniform hardness and microstructures across the weld restored area.
Corus’ new patented repair technique includes four steps.
The defect is first removed by using a portable three axis rail milling machine that clamps onto the sides of the rail. It ensures a consistent excavation of the identified defect. This is itself a significant improvement on the use of manual grinding or flame scarfing, both of which do not give a consistent cavity shape or surface finish to facilitate automatic programmed welding.
Secondly, the adjacent area and the cavity are preheated with a conventional burner. For Grade 260 rails, the prescribed temperature is between 60 and 80°C. The choice of this temperature is for the control of the microstructure in the HAZ and the programmed square weave pattern of deposition of the subsequent/adjacent beads ensures that the microstructure in the HAZ is fine pearlite and free of any embrittling martensite. This temperature is suitable for the vast majority of high carbon rail steels in use today but it may need to be modified for steels that have different transformation characteristics such as low carbon carbide free bainitic steels.
The third stage uses a semi automatic weld repair machine, with an open arc welding process, a Network Rail (UK) approved TN3-0 welding consumable and prescribed welding parameters. The positioning of the top layer is crucial to prevent the creation of a new Heat Affected Zone (HAZ). Most of the top weld layer is partially removed by profile grinding.
The fourth and last step consists of restoring and blending the transverse and longitudinal rail profile by grinding, using conventional rail grinders.
A comparative evaluation of the existing MMA technique and the new process was achieved by recording the thermal history of both processes using embedded thermocouples. Several key conclusions demonstrates the metallurgical robustness of the process:
-Despite the use of just 80°C preheat, the temperature in the HAZ after each deposited weld bead remains above 200°C, preventing any transformation to the martensitic microstructure (as the martensite start temperature is 160°C for grade 260 rails).
-The cooling rates in the developed process are almost identical to those in the conventional MMA process for all deposition passes except the first. The faster rate of 5.2 °C/s after the first weld bead is also half the critical rate for transformation to martensite.
-A crack free weld deposit interface is apparent with a fully pearlitic microstructure, free from martensite and bainite.
-The hardness profile shows that the wear resistance of the bainitic weld deposit will be comparable to that of grade R260 parent rail and ensure a good longitudinal profile.
-The weld deposit was subjected to a bending fatigue test with an applied stress range equivalent to three times that expected in service. Five million cycles were successfully completed without any failure. The same deposit successfully endured a further 4.3 million cycles at an applied stress range equivalent to eight times that expected in service.
The running of carriage wheels on rails creates high and complex stress patterns within the rail/wheel contact patch, leading to surface degradation. The wide range of track design, wheel profiles, and types of traffic can result in a variety of surface defects that reduces the life of the rail. Defects such as squats and wheelburns occur even in the most modern and well maintained railway networks and, as a broad general rule, every network develops one such defect each year, every two kilometres. The replacement of such defects with a short rail section is expensive and not always desirable as it introduces two new discontinuities in the track in the form of two aluminothermic welds (exothermic reaction using aluminium as the reducing agent) that destroy the advantages obtained with long hot-rolled rail (up to 120 metres). The alternative conventional technique for the repair of such defects is the Manual Metal Arc (MMA) welding process. Although the technique is used many industries, it is heavily reliant on the competence of the welder, is time consuming, and is prone to internal defects such as porosity that subsequently grow through fatigue, and if not detected by ultrasonic inspection, result in rail breaks.
The following factors contribute to the cost effectiveness and technical robustness of the new developed process:
1.The move away from the conventional preheating temperature of 350°C to just 80°C has the advantage of faster repair, reduced depth of heat affected zone, and more robust microstructure.
2.The use of a standardized removal of the defect area by controlled milling has the advantage of reproducibility and removes the subjective judgement of the operator.
3.The use of a semi-automatic programmed open arc welding process with flux cored arc wire ensures control of heat input and predictable operational times.
The quality of the weld restored running surface from the developed process is ensured as the repair is extremely resistant to fatigue and has similar wear resistance to that of the standard Grade R260 rail with uniform hardness and microstructures across the weld restored area.
Corus’ new patented repair technique includes four steps.
The defect is first removed by using a portable three axis rail milling machine that clamps onto the sides of the rail. It ensures a consistent excavation of the identified defect. This is itself a significant improvement on the use of manual grinding or flame scarfing, both of which do not give a consistent cavity shape or surface finish to facilitate automatic programmed welding.
Secondly, the adjacent area and the cavity are preheated with a conventional burner. For Grade 260 rails, the prescribed temperature is between 60 and 80°C. The choice of this temperature is for the control of the microstructure in the HAZ and the programmed square weave pattern of deposition of the subsequent/adjacent beads ensures that the microstructure in the HAZ is fine pearlite and free of any embrittling martensite. This temperature is suitable for the vast majority of high carbon rail steels in use today but it may need to be modified for steels that have different transformation characteristics such as low carbon carbide free bainitic steels.
The third stage uses a semi automatic weld repair machine, with an open arc welding process, a Network Rail (UK) approved TN3-0 welding consumable and prescribed welding parameters. The positioning of the top layer is crucial to prevent the creation of a new Heat Affected Zone (HAZ). Most of the top weld layer is partially removed by profile grinding.
The fourth and last step consists of restoring and blending the transverse and longitudinal rail profile by grinding, using conventional rail grinders.
A comparative evaluation of the existing MMA technique and the new process was achieved by recording the thermal history of both processes using embedded thermocouples. Several key conclusions demonstrates the metallurgical robustness of the process:
-Despite the use of just 80°C preheat, the temperature in the HAZ after each deposited weld bead remains above 200°C, preventing any transformation to the martensitic microstructure (as the martensite start temperature is 160°C for grade 260 rails).
-The cooling rates in the developed process are almost identical to those in the conventional MMA process for all deposition passes except the first. The faster rate of 5.2 °C/s after the first weld bead is also half the critical rate for transformation to martensite.
-A crack free weld deposit interface is apparent with a fully pearlitic microstructure, free from martensite and bainite.
-The hardness profile shows that the wear resistance of the bainitic weld deposit will be comparable to that of grade R260 parent rail and ensure a good longitudinal profile.
-The weld deposit was subjected to a bending fatigue test with an applied stress range equivalent to three times that expected in service. Five million cycles were successfully completed without any failure. The same deposit successfully endured a further 4.3 million cycles at an applied stress range equivalent to eight times that expected in service.