www.industrymiddleeast.com
11
'10
Written on Modified on
Alufast® fasteners facilitate lightweight construction
Alufast® aluminium screws from Arnold Umformtechnik are especially advantageous for joining magnesium components: transmission, housing, load-bearing, stiffening... Especially with material pairs exposed to thermal stress, they significantly enhance the security of threaded fastener joints. Furthermore, Alufast® aluminium screws weigh only one-third as much as equivalent steel screws. Particularly with large volumes the weight savings can amount to the equivalent of several metric tons of steel per year.
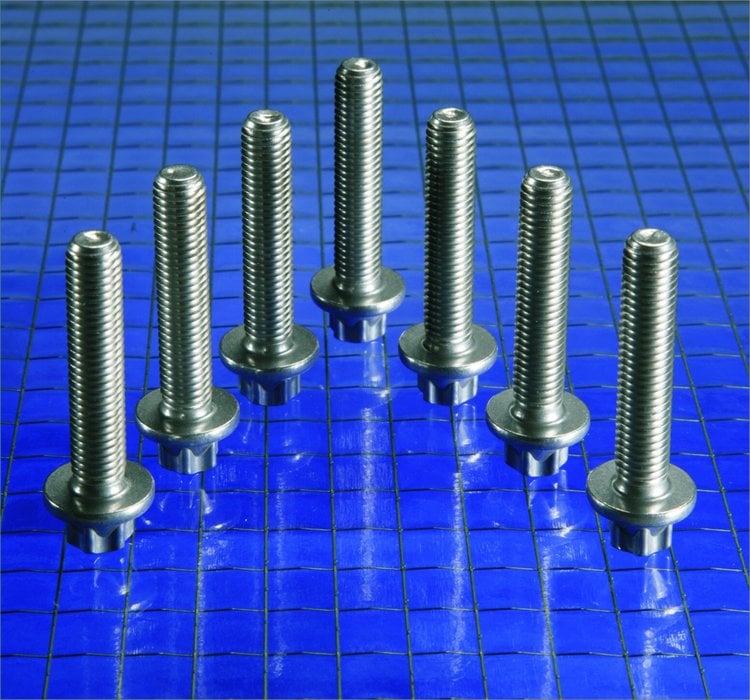
The type 6056 aluminium alloy used for Alufast fasteners has a proven track record of durability for joining magnesium components with threaded fasteners. The Alufast® product line has good characteristics for thermal expansion, corrosion resistance and recycling. At the same time, Alufast® products fulfil stringent requirements for retention of clamping force, thermal stability and weight reduction. Alufast® products are especially suitable for joining magnesium components exposed to thermal stress and corrosion stress. The choice of type 6056 aluminium alloy and suitable heat treatment ensure that the screws reliably provide the specified strength and strain characteristics. Unlike steel screws, which require overdimensioned head bearing areas for joining magnesium components, standard dimensions are sufficient with Alufast® fasteners.
Alufast® fasteners also exhibit good corrosion characteristics in contact with magnesium. The relatively small difference in electromotive force significantly reduces the risk of corrosion compared with steel fasteners. The mechanical properties of the screws are practically stable under long-term stress at temperatures up to approximately 150 °C. Brief temperature excursions up to approximately 180 °C do not pose a risk. Alufast® screws can be used untreated in combination with commonly used magnesium casting alloys, such as Az91 HP. They do not need any additional surface coating. The corrosion resistance of the components remains stable over their entire operating life.
Relaxation processes, in particular in the joined magnesium components, can lead to reduced clamping forces, especially in joints exposed to thermal stress. Particularly in applications such as engines and transmissions, the component temperature range of -30 °C to 150 °C leads to temperature differences of up to 180 °C. In joints with steel screws, the high temperatures initially cause additional stress on the threaded fastener joint due to thermal expansion, which usually leads to relaxation or even plastification of the magnesium. These relaxation effects in magnesium lead directly to reduced clamping force at elevated operating temperatures. With a thermal expansion coefficient similar to that of magnesium, Alufast® screws exhibit significantly less loss of clamping force with temperature cycling than conventional steel screws.
Alufast® aluminium screws weigh only one-third as much as equivalent steel screws. The weigh savings in a transmission application with 20 screws per transmission can be as much as 340 grams. Even greater weight savings can be achieved because the screw length can be reduced considerably with Alufast® fasteners without compromising joint quality.
Images:
ALUFAST 1: Alufast fasteners
ALUFAST 2: Alufast (left) reduces the risk of corrosion compared with steel fasteners (right)
Alufast® fasteners also exhibit good corrosion characteristics in contact with magnesium. The relatively small difference in electromotive force significantly reduces the risk of corrosion compared with steel fasteners. The mechanical properties of the screws are practically stable under long-term stress at temperatures up to approximately 150 °C. Brief temperature excursions up to approximately 180 °C do not pose a risk. Alufast® screws can be used untreated in combination with commonly used magnesium casting alloys, such as Az91 HP. They do not need any additional surface coating. The corrosion resistance of the components remains stable over their entire operating life.
Relaxation processes, in particular in the joined magnesium components, can lead to reduced clamping forces, especially in joints exposed to thermal stress. Particularly in applications such as engines and transmissions, the component temperature range of -30 °C to 150 °C leads to temperature differences of up to 180 °C. In joints with steel screws, the high temperatures initially cause additional stress on the threaded fastener joint due to thermal expansion, which usually leads to relaxation or even plastification of the magnesium. These relaxation effects in magnesium lead directly to reduced clamping force at elevated operating temperatures. With a thermal expansion coefficient similar to that of magnesium, Alufast® screws exhibit significantly less loss of clamping force with temperature cycling than conventional steel screws.
Alufast® aluminium screws weigh only one-third as much as equivalent steel screws. The weigh savings in a transmission application with 20 screws per transmission can be as much as 340 grams. Even greater weight savings can be achieved because the screw length can be reduced considerably with Alufast® fasteners without compromising joint quality.
Images:
ALUFAST 1: Alufast fasteners
ALUFAST 2: Alufast (left) reduces the risk of corrosion compared with steel fasteners (right)