www.industrymiddleeast.com
08
'11
Written on Modified on
Safety Rotary Encoder RVK58S : SIL3/PLe compliant drive solutions, including rotor position detection
Machine and plant engineering companies are increasingly relying on failsafe components to fulfil the safety requirements specified in the current version of the Machinery Directive 2006/42/EC. The safety sine/cosine rotary encoder RVK58S is an ideal choice as it also allows the position of the motor rotor to be detected with the highest accuracy levels.
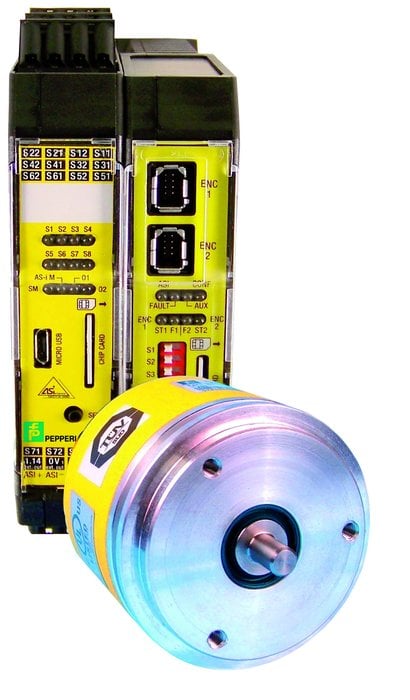
Only rigorous end-to-end safety concepts are able to truly ensure the required safety level. This means that the capability of a safety solution is effectively only as good as the weakest link in the chain. It has long been common practice to configure important system components redundantly and detect potential malfunctions by comparing corresponding system parameters. Although this fulfils the purpose, it is undesirable in today’s view due to duplication of the costs of equipment and material as well as high installation and cabling efforts. Furthermore, increasing the number of components raises the probability of failure and makes certification of conformity more expensive.
Self-monitoring replaces redundancy
Intelligent self-monitoring is often used now in place of redundancy to ensure proper operation of the various functional units. The new RVK58S sine/cosine rotary encoder from Pepperl+Fuchs Drehgeber GmbH, plays a key role in the development of safe drive solutions. This high-resolution encoder, packaged in a 58-mm housing, has 1024 increments per revolution and boasts a functional safety concept, along with an absolute position track as an extra feature. Signal conditioning is handled by a special ASIC, which also looks after internal diagnostics.
Faults on the incremental encoder disc or errors in the signal path can be detected reliably by using the formula sin²(x) + cos²(x) = 1 to evaluate the incremental sine and cosine signals from the encoder, which are offset by 90 degrees. The supply voltage, temperature, LED drive and calibration data checksum are also monitored. If a violation occurs, the encoder electronics put the outputs in a high-impedance state so that the controller can detect the malfunction immediately by means of its open-circuit detection function. With this feature, the new rotary encoder considerably simplifies the development of safe machines and at the same time eliminates the need for the redundant sensor component approach used in conventional concepts. The sine/cosine rotary encoder is already certified, and certification of the additional absolute position track is currently underway at TÜV. After this certification is issued, the device will be approved for use in drive products that fulfil safety requirements up to SIL3/PLe using only one encoder.
Rotor position detection using a single-cycle absolute position track
In addition to the high-resolution incremental tracks, the rotary encoder has a sine/cosine absolute position track with exactly one cycle per revolution. It provides information on the actual position of the rotor in the motor. This information is needed for purposes such as start-up commutation of synchronous motors. The absolute position is output as a digitized signal with 13-bit resolution using either the Synchronous Serial Interface (SSI) or Bidirectional Synchronous Serial (BiSS) interface protocol. With the combination of the sine/cosine interface, SSI and BiSS, the encoder utilizes existing communication paths and eliminates the need for proprietary safety protocols.
In combination with a suitably certified controller, the safety rotary encoder from Pepperl+Fuchs enables single-encoder solutions, eliminating the need to integrate a second encoder to fulfil more stringent safety requirements. However, a prerequisite for this is that both sensor channels are always connected to the controller. With this system configuration, classification at a higher ISO 13849 performance level (PL e) or IEC 62061 safety integrity level (SIL 3) is straightforward. All motor activities are carried out and monitored reliably, enabling the implementation of typical speed-based safety functions such as safe limited speed, safe speed monitoring, safe standstill monitoring, safe rotation direction, safe acceleration/deceleration, and so on.
Safety rotary encoder replaces mechanical safety solutions
The innovative safety functions allow conventional mechanical safety devices, which are subject to wear, to be replaced by software functions in many applications. For example, in high-bay warehouses the expensive hydraulic end-stop buffers at the ends of the storage and retrieval machine guideways can be eliminated entirely. In addition, less empty space is needed and the vehicles can be made lighter thanks to lower braking deceleration. In combination with a suitable safety control unit installed either locally or in the drive controller, the RVK58S monitors compliance with the specified braking ramp (safety limited deceleration) as well as the speed of travel (safe limited speed) of the storage and retrieval machine. If any of the configured limits is exceeded, the system is either braked with the aid of the drive or (in case of total drive failure) a mechanical brake in the vehicle is applied.
Safety functions simplify start-up and servicing
Machine operators are most likely to be injured during start-up, set-up and servicing, since these activities are usually performed directly in the hazard area. The safety rotary encoder enables the implementation of many extended safety functions that allow these activities to be managed safely with minimal effort.
Summary
Machine manufacturers and operators are obliged to fulfil the safety requirements specified in EN ISO 13849, and the world’s first functionally safe rotary encoder with a supplementary absolute position track makes a valuable contribution to the efficient implementation of safe drive solutions. The RVK58S merges seamlessly with modern safety concepts and makes it easier for machine and plant engineering companies to demonstrate that their products conform to the required performance level (PL) or safety integrity level (SIL). Thanks to the integrated absolute position track, the encoder is suitable for general-purpose use in a wide variety of drive solutions, regardless of whether they are based on synchronous or asynchronous motors.
Self-monitoring replaces redundancy
Intelligent self-monitoring is often used now in place of redundancy to ensure proper operation of the various functional units. The new RVK58S sine/cosine rotary encoder from Pepperl+Fuchs Drehgeber GmbH, plays a key role in the development of safe drive solutions. This high-resolution encoder, packaged in a 58-mm housing, has 1024 increments per revolution and boasts a functional safety concept, along with an absolute position track as an extra feature. Signal conditioning is handled by a special ASIC, which also looks after internal diagnostics.
Faults on the incremental encoder disc or errors in the signal path can be detected reliably by using the formula sin²(x) + cos²(x) = 1 to evaluate the incremental sine and cosine signals from the encoder, which are offset by 90 degrees. The supply voltage, temperature, LED drive and calibration data checksum are also monitored. If a violation occurs, the encoder electronics put the outputs in a high-impedance state so that the controller can detect the malfunction immediately by means of its open-circuit detection function. With this feature, the new rotary encoder considerably simplifies the development of safe machines and at the same time eliminates the need for the redundant sensor component approach used in conventional concepts. The sine/cosine rotary encoder is already certified, and certification of the additional absolute position track is currently underway at TÜV. After this certification is issued, the device will be approved for use in drive products that fulfil safety requirements up to SIL3/PLe using only one encoder.
Rotor position detection using a single-cycle absolute position track
In addition to the high-resolution incremental tracks, the rotary encoder has a sine/cosine absolute position track with exactly one cycle per revolution. It provides information on the actual position of the rotor in the motor. This information is needed for purposes such as start-up commutation of synchronous motors. The absolute position is output as a digitized signal with 13-bit resolution using either the Synchronous Serial Interface (SSI) or Bidirectional Synchronous Serial (BiSS) interface protocol. With the combination of the sine/cosine interface, SSI and BiSS, the encoder utilizes existing communication paths and eliminates the need for proprietary safety protocols.
In combination with a suitably certified controller, the safety rotary encoder from Pepperl+Fuchs enables single-encoder solutions, eliminating the need to integrate a second encoder to fulfil more stringent safety requirements. However, a prerequisite for this is that both sensor channels are always connected to the controller. With this system configuration, classification at a higher ISO 13849 performance level (PL e) or IEC 62061 safety integrity level (SIL 3) is straightforward. All motor activities are carried out and monitored reliably, enabling the implementation of typical speed-based safety functions such as safe limited speed, safe speed monitoring, safe standstill monitoring, safe rotation direction, safe acceleration/deceleration, and so on.
Safety rotary encoder replaces mechanical safety solutions
The innovative safety functions allow conventional mechanical safety devices, which are subject to wear, to be replaced by software functions in many applications. For example, in high-bay warehouses the expensive hydraulic end-stop buffers at the ends of the storage and retrieval machine guideways can be eliminated entirely. In addition, less empty space is needed and the vehicles can be made lighter thanks to lower braking deceleration. In combination with a suitable safety control unit installed either locally or in the drive controller, the RVK58S monitors compliance with the specified braking ramp (safety limited deceleration) as well as the speed of travel (safe limited speed) of the storage and retrieval machine. If any of the configured limits is exceeded, the system is either braked with the aid of the drive or (in case of total drive failure) a mechanical brake in the vehicle is applied.
Safety functions simplify start-up and servicing
Machine operators are most likely to be injured during start-up, set-up and servicing, since these activities are usually performed directly in the hazard area. The safety rotary encoder enables the implementation of many extended safety functions that allow these activities to be managed safely with minimal effort.
Summary
Machine manufacturers and operators are obliged to fulfil the safety requirements specified in EN ISO 13849, and the world’s first functionally safe rotary encoder with a supplementary absolute position track makes a valuable contribution to the efficient implementation of safe drive solutions. The RVK58S merges seamlessly with modern safety concepts and makes it easier for machine and plant engineering companies to demonstrate that their products conform to the required performance level (PL) or safety integrity level (SIL). Thanks to the integrated absolute position track, the encoder is suitable for general-purpose use in a wide variety of drive solutions, regardless of whether they are based on synchronous or asynchronous motors.