www.industrymiddleeast.com
01
'11
Written on Modified on
Increased flexibility and a 30% gain in productivity
New turning and milling centre for heavy-duty series production.
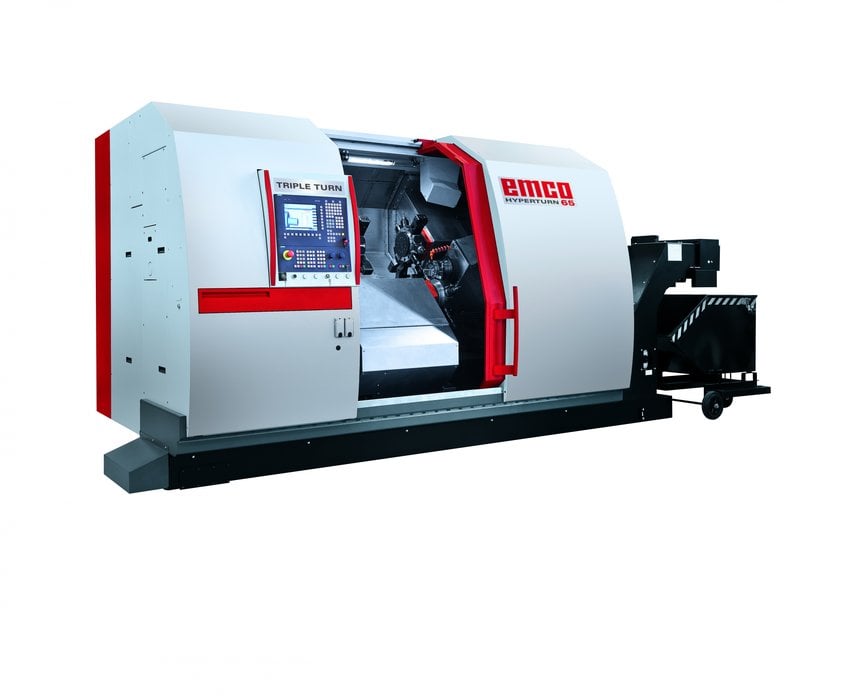
The new Hyperturn family from Emco now has another, particularly high-performance member: the heavy-duty turning and milling centre Hyperturn 65-TT. Up to three tool turrets increase productivity by 30% or more compared to its already highly efficient predecessors. The third turret has additional technical and economic benefits: the use of at least 36 (rather than 24) tool stations increases flexibility when machining complex work pieces, reduces setup time, and creates capacity for spare tools. The new Hyperturn 65-TT also includes three Y-axes for demanding and complex milling work in the main and counter spindle. Performance is likewise increased through the enhanced user interface, comprehensive technology cycles, and, above all, the use of virtual Hyperturn for optimized order processing, programming, and the simulation of all work operations in parallel with the actual, fully productive turning and milling centre.
The Hyperturn 65 also comes in a Duoturn design with 2 tool turrets. The second Y-axis allows high flexibility when milling complex workpieces. In contrast to the Hyperturn 665, the opposing arrangement of the turrets creates numerous options for boring. The Hyperturn 65 Tripleturn and Duoturn ident do not have the third turret (see technical data).
The Hyperturn 65 also comes in a Duoturn design with 2 tool turrets. The second Y-axis allows high flexibility when milling complex workpieces. In contrast to the Hyperturn 665, the opposing arrangement of the turrets creates numerous options for boring. The Hyperturn 65 Tripleturn and Duoturn ident do not have the third turret (see technical data).
All 36 driven tools work at speeds of up to 5,000 rpm with traverse paths in the Y-axis of 100 mm. Together with the identical performance offered by the main and counter spindle (max. 29 kW and 5,000 rpm), users benefit from the optimal combination of technical machining options and cost-effectiveness. This is complemented by the increased spindle distance of 1,300 mm and the resulting increase in working space, which provides improved freedom of movement and reduces the likelihood of collisions when working with three tools simultaneously. The 65 mm bore spindles are structurally identical and enable the loading and unloading of bars or longer work-pieces; optionally up to Ø77 mm.
In addition to mechanical and electrical performance values, control systems and software are increasingly determining the productive efficiency of machine tools.
Emco has therefore fitted the Hyperturn 65 with the new Sinumerik 840 D-sl control unit from Siemens. The advanced user interface makes the machine intuitive to operate and easy to program. Emco CPS Pilot also makes a significant contribution to long-term capacity utilization and, therefore, to further increases in productivity. This program enables users to work on a virtual Hyperturn 65 independently of the production model, which can be used to carry out complete programming, process orders, select and test tools, simulate work processes, and identify potential collisions in advance. Once everything is running as required on the virtual Hyperturn, the complete work process can be transferred to the actual Hyperturn 65 via a USB interface. This process dramatically reduces machine downtime and the risk of collisions for multislide lathes.
The product refinements and their synergies have also resulted in improved dynamics, increased performance, and higher energy efficiency. All of which validates Emco's strategy of manufacturing machines "in the heart of Europe."
In addition to mechanical and electrical performance values, control systems and software are increasingly determining the productive efficiency of machine tools.
Emco has therefore fitted the Hyperturn 65 with the new Sinumerik 840 D-sl control unit from Siemens. The advanced user interface makes the machine intuitive to operate and easy to program. Emco CPS Pilot also makes a significant contribution to long-term capacity utilization and, therefore, to further increases in productivity. This program enables users to work on a virtual Hyperturn 65 independently of the production model, which can be used to carry out complete programming, process orders, select and test tools, simulate work processes, and identify potential collisions in advance. Once everything is running as required on the virtual Hyperturn, the complete work process can be transferred to the actual Hyperturn 65 via a USB interface. This process dramatically reduces machine downtime and the risk of collisions for multislide lathes.
The product refinements and their synergies have also resulted in improved dynamics, increased performance, and higher energy efficiency. All of which validates Emco's strategy of manufacturing machines "in the heart of Europe."