www.industrymiddleeast.com
13
'12
Written on Modified on
EPLAN Platform increases the speed of process at the company W. Althaus AG by 30%
Swiss company W. Althaus AG, a full-service provider for industrial automation that delivers around 5000 switch cabinets per year all over the world, uses the EPLAN platform as the backbone for data consistency. The recent migration to EPLAN Pro Panel, the 3D system for switchgear construction brought about a quantum leap in terms of process optimisation.
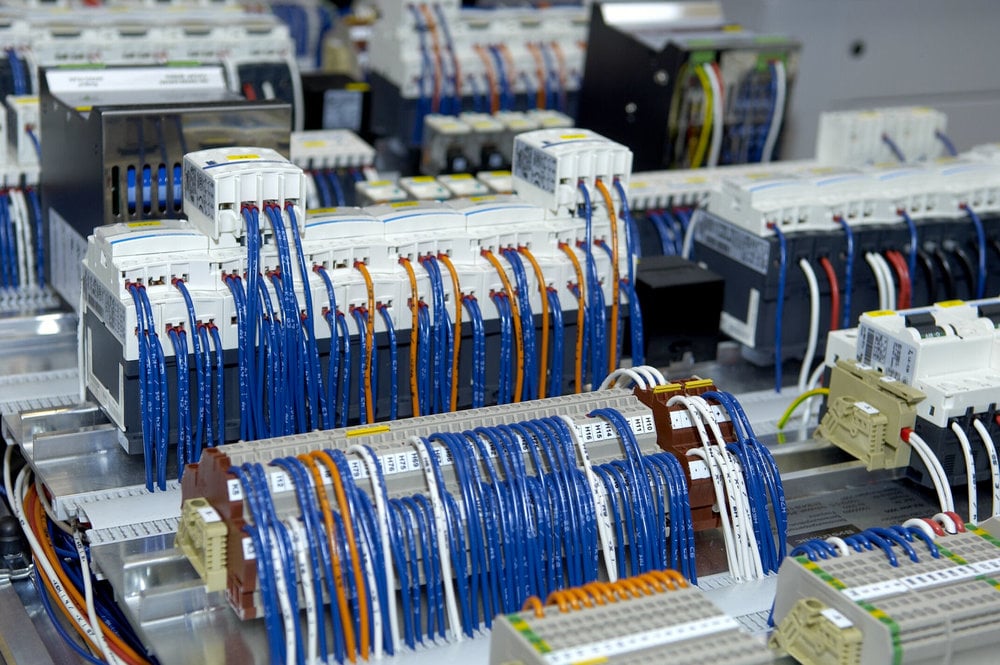
Every year, the industrial automation specialists from W. Althaus AG in Switzerland deliver around 5000 switch cabinets, from single and serial control units to prototypes, and around 800 small control units all over the world. The fully automated float glass production line in South Korea with round-the-clock availability is just as much a part of the customer portfolio as Swiss solar systems or conveyor systems in the food industry. The family-run company boasts around 110 employees and provides a comprehensive range of services, from project planning, hardware and software development to delivery, commissioning and final acceptance. Control cabinets, terminal strips, operating panels and control panels are all manufactured in-house, in a production area that is more than 6000m² in size. Cable and wire fabrication also takes place in-house. The Althaus designers deal with all electrical engineering using EPLAN Electric P8 and EPLAN Pro Panel, the 3D system for switchgear construction.
Integrative processes, including 3D data
"We do not make any demands of our customers with regard to the materials and components that are used or the integration of device control units," explains Marco Schneider, Company Manager of W. Althaus AG. However, this requires careful maintenance of complex product databases, which is easy to accomplish with EPLAN: The material data of the majority of manufacturers can be imported directly in 3D, and synchronisation with customer databases can be carried out even more effectively using a solution that has been programmed in-house.
With ATHAS, the "Althaus Terminal Handling System", the company has developed a manufacturer-independent universal solution for the automatic production of terminal strips using robots based on EPLAN Pro Panel. This is now being offered to terminal suppliers and other switch cabinet manufacturers.
"We are committed to achieving the highest degree of automation possible," says Schneider. For him, the EPLAN platform is therefore not just engineering and ECAD software, but the data consistency backbone within the company. Projects that have already been completed can be retrieved from the databases and reused. Predefined modules, components and sub-projects, including the necessary items and materials, can be stored in the EPLAN database as macros and transferred to follow-up projects. The ERP system is also linked to EPLAN – the automatically generated and adapted bills of materials mean that materials that are no longer available in the company's own warehouse can be ordered in good time and exactly in accordance with requirements.
New dimension: EPLAN Pro Panel
The migration of EPLAN Cabinet to the new EPLAN Pro Panel – W. Althaus AG was one of the first Swiss companies to introduce this – brought a quantum leap with regard to process optimisation. With EPLAN Pro Panel the company is now consistently working with 3D data throughout the EPLAN Platform. To Roland Ackermann, head of electrical engineering, the advantages are obvious – the EPLAN Platform has now been optimally integrated, the removal of previously required intermediate steps during data transfers has saved time and avoided mistakes, performance capability has improved significantly and operation has become easier, even for beginners. "Simulation has become better because of the 3D graphics, you can see immediately what has to go where, and collision points can be avoided from the outset," said Ackermann. Above all, he and his team can work much more flexibly. “Because all project disciplines are networked on a uniform data basis and changes and updates are registered consistently through to the bills of materials, I can also start with the device-based mounting layout and transfer over the information for the circuit diagram and the connection definition later – almost like Windows, using Drag&Drop."
Consistent through to production
Operations manager Marco Schneider particularly appreciates the communication strength of the EPLAN solutions. In metalworking, for example, for flat mounting plates, Althaus uses a fast laser cutting machine with a thread cutting head as an unusual additional, as well as a 4-axis CNC machining centre for plate, box and housing machining. The machining data that is required is generated in EPLAN Pro Panel and read directly into the machine control unit. Not just electrical diagrams, material lists, terminal plans and layout plans have to be generated using EPLAN, but also the machining data for the systems that cut channels and rails to length, the wiring assistant and the previously mentioned automatic terminal strip assembly machines. The automatic cable fabrication system also receives the information that is needed about cable lengths, wires, bundling and labelling directly from EPLAN on the basis of the circuit diagram and the 3D cable routing data, and uses it to create cable bundles that are ready for installation and clearly labelled. "When our production employees start with the layout, everything is there and pre-equipped; they basically assemble a "construction kit" and do not have to spend time looking for materials and jobs in the assembly plans," summarises Schneider.
This ability pays for itself even in single quantities and it increases the pace and eliminates mistakes, explains the operations manager. In addition, time-consuming and expensive corrections can be avoided and personnel can be deployed more flexibly. This high degree of preparation means that repeated and routine tasks can also be carried out by non-specialist employees. At Althaus the employees work in teams and deal with layouts, wiring and quality control; testing takes place manually and automatically with the aid of the "Panel Scout" test control unit which has been developed in-house.
Speed of process increased by 30%
The standardisation and automation of processes, which should be as extensive as possible, has reduced throughput times within the company by approximately a third by using the EPLAN platform, estimates Schneider.
More information:
www.eplan.de
www.althaus-ag.ch
Pictures: (Source: W. Althaus.AG)
bild1.jpg:
Standardised processes: Electrical diagrams, terminal and layout plans are generated via the EPLAN Platform.
bild2.jpg:
Assembled by robots: Automatic manufacture of terminal strips with the "ATHAS" flexible handling system.
bild3.jpg:
Quantum leap: With EPLAN Pro Panel, the Althaus engineers design switchgear more effectively and flexibly.
bild4/5jpg:
Althaus provides a range of services, from project planning, hardware development and software development to the assembly and commissioning of switch cabinets.
bild6.jpg:
Bespoke switch cabinets: Althaus doesn‘t make any demands of its customers with regard to the materials and device control units that are used.
Schneider_neu.jpg:
Operations manager Marco Schneider in front of the switch cabinets
screen1.jpg:
EPLAN Pro Panel brings 3D into the project.
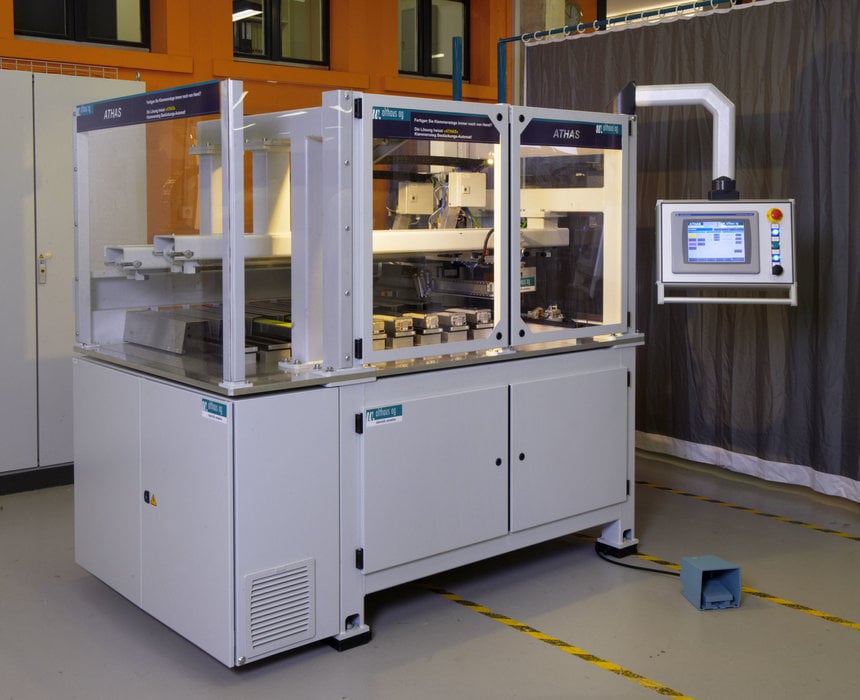
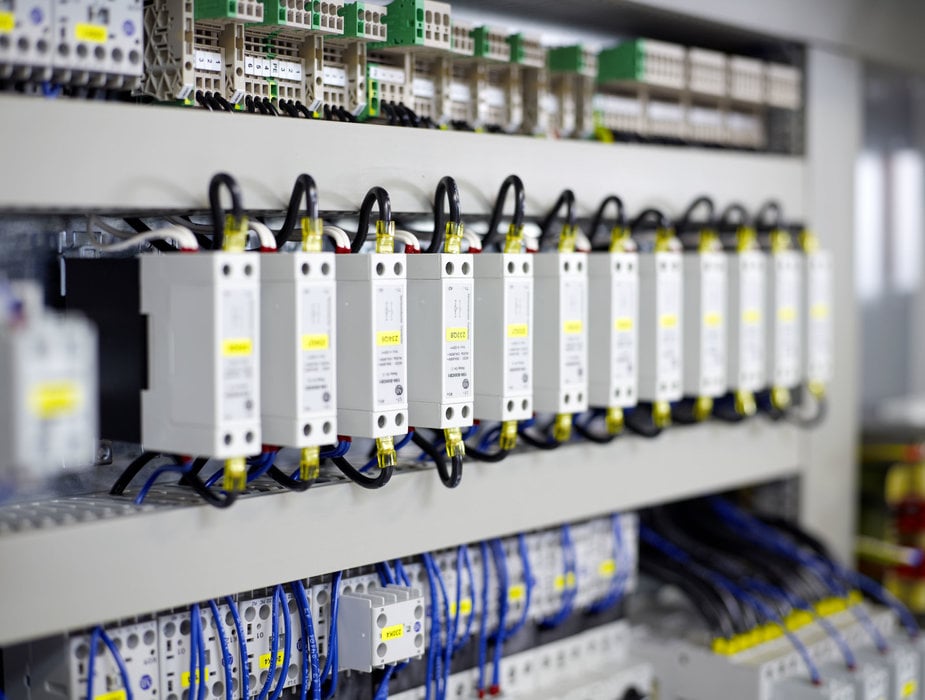
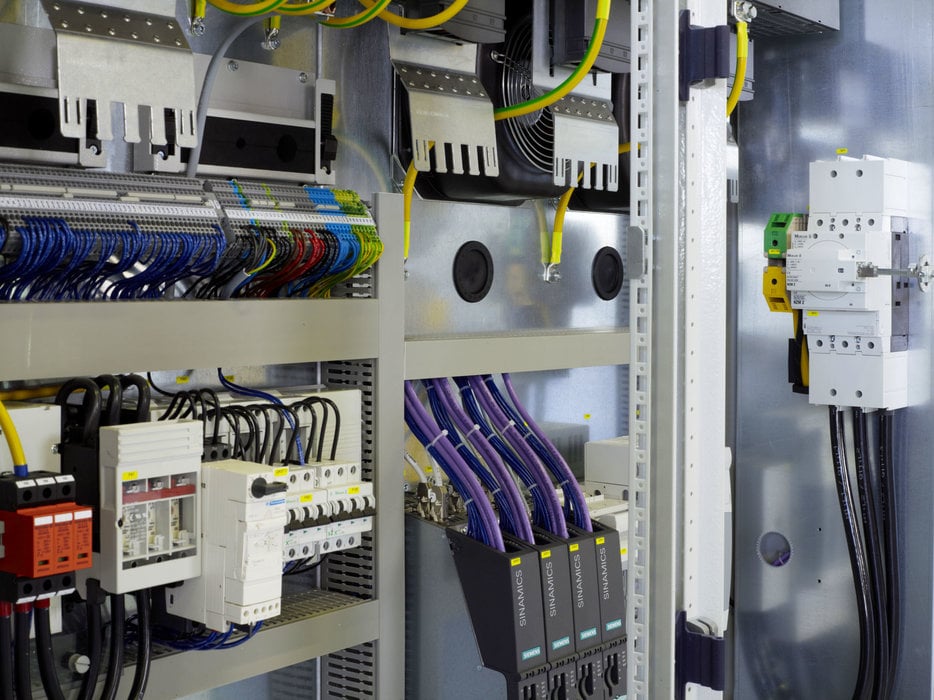
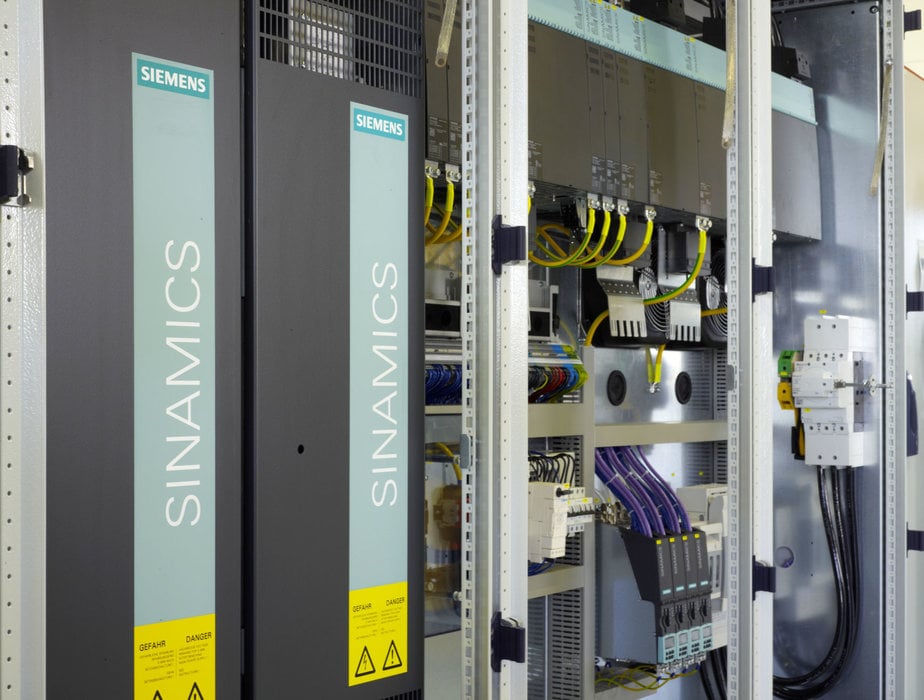
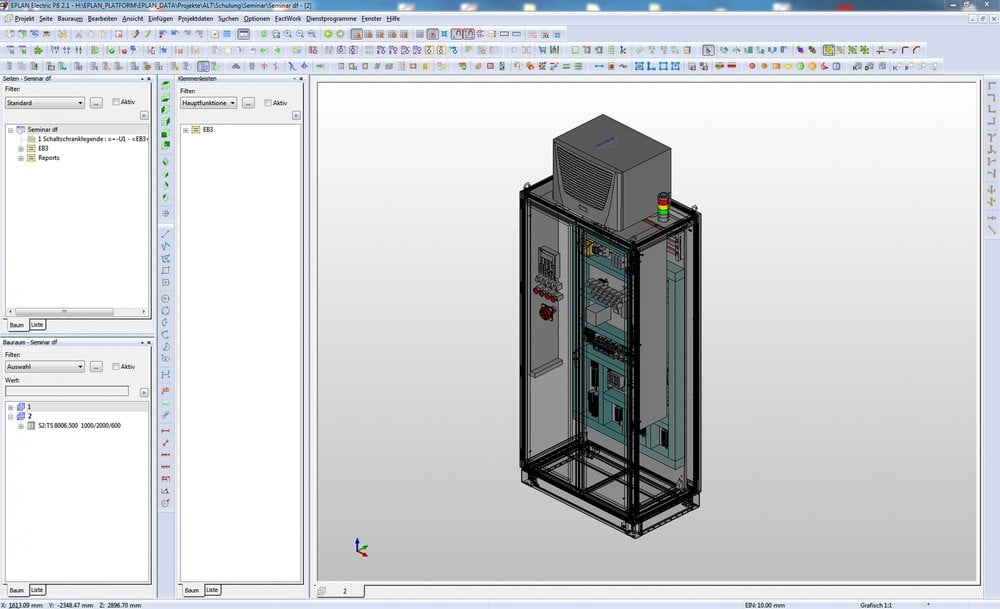