www.industrymiddleeast.com
20
'12
Written on Modified on
Kennametal Introduces the New Mill 1-7 High-Performance Shoulder Mill for Small Diameters
As the latest complement to the Mill 1™ platform for finishing operations, Mill 1-7™ is Kennametal’s solution for finishing in small diameter milling. This new line is specifically engineered to cover ramping, slotting, and plunging for aerospace, energy, and general engineering applications. Mill 1-7 is a diverse tool for roughing and finishing operations, where small diameter end mills are required.
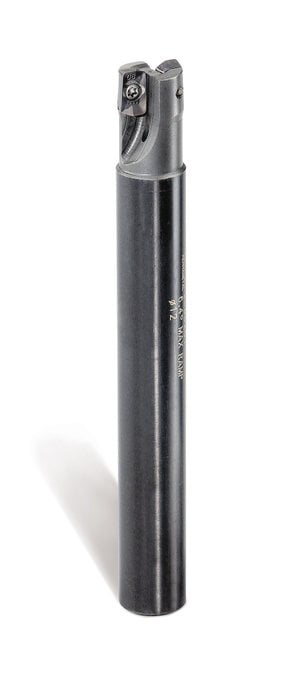
Mill 1-7 inserts are designed with elliptical cutting edges that are optimized with a straight 90° wall and true 0° lead, making them capable of replacing SCEM finish machining in certain applications.
Mill 1-7 inserts come in three grades to cover various applications and conditions:
- The KC725M™ grade for general and heavy steel, stainless steel, and ductile cast iron milling applications is engineered for both wet and dry machining.
- The multilayered TiN-TiCN-Al2O3-CVD-coated KCPK30™ grade has advanced Beyond™ post-coat treatment for a wide application area in general and rough milling of steels and cast irons. This grade works best dry but functions under wet conditions.
- The KC522M™ grade is engineered to provide better performance in general machining of high-temperature alloys and stainless steel. KC522M resists breakage and offers improved wear resistance and increased strength.