www.industrymiddleeast.com
26
'12
Written on Modified on
Canadian Natural resources automates oil and gas operations using PcVue Solutions from Arc Informatique.
CNRL is measuring millions of tags and an approximate 800,000 I/O points within its primary operations. GE and Allen-Bradley PLCs, Fisher and Bristol Babcock RTUs are the major brands used throughout production. The pcVue SCADA is monitoring and providing pertinent data used by some 2,500 employees who need to access the information in some shape or form – i.e., monitoring, reviewing, or maintaining data in real-time.
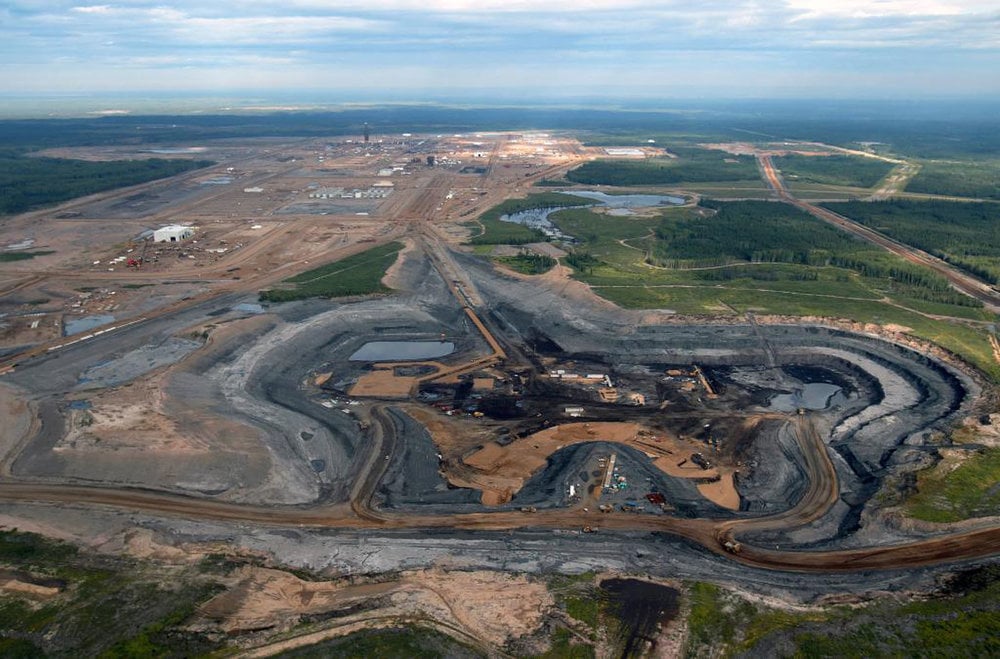
The company operates its business through three primary reportable segments: Horizon oil sands production, thermal heavy oil, and conventional oil and gas. Within the last year, CNRL invested in a large scale automation project that primarily impacts the conventional oil and gas business that deals with the exploration, development, production and marketing of crude oil, natural gas liquids and natural gas.
Canadian Natural Resources needed a better way to manage the process control and monitoring of its 300 gathering stations, 800 compressor stations, and 150 gas processing facilities. CNRL’s SCADA Specialist, Kurtis Jackson, spearheaded the company’s automation project to replace its FactoryLink SCADA systems with the pcVue’s SCADA and FrontVue solutions. CNRL has numerous independent automation systems of various brands and Jackson wanted to centralize and achieve consistency by integrating as many of these automation systems as possible on pcVue. In addition, CNRL wanted to leverage pcVue’s ability to support multi-station architectures for networking and currently runs Modbus Roc, Roc Talk, and BSAP.
The replacement process started about eight months ago when CNRL began migration of their FactoryLink SCADA to pcVue using the Smart Generator. This pcVue tool can easily and automatically convert a very high proportion of their existing applications to pcVue, while ensuring maximum compatibility and security. “For most of our SCADA applications we were upgrading, between 60-80% of our FactoryLink applications converted to pcVue with ease. This saved us a tremendous amount of time with not having to reconfigure the entire applications and it meant that we did not have to retrain our users. It also says that we are investing in our future with SCADA automation,, pcVue regularly enhances its SCADA with version updates and new features,” said Jackson.
“We run daily our production reports and utilize real-time and historical trending to give us the data needed to make sure we have met our production goals and will meet our sales contracts, such as to a pipeline company for example,” said Jackson. Currently, Kurtis has already implemented eight pcVue servers with remote client access and expects to deploy approximately 40 pcVue SCADA systems within the next two years.
CTH Systems Inc., a value-added reseller of pcVue, helped to configure and facilitate the migration to pcVue. Using Smart Generator, the engineers were able to convert all of the graphical elements (mimics, symbols and templates), local and shared libraries (symbols, pictures), all sets of variables for the application (including variable tables, alarm configurations and histories) and the database without any rework. It also converts the TCP/IP communication objects and their links. “We were really happy with how easy it was to transfer all of our applications to pcVue in a very easy, straightforward manner,” said Jackson.
In addition, CNRL uses CTH Systems’ IM-SCADA™, a multiprotocol measurement and communication software. It allows the wells that are equipped with different automation devices, such as RTUs (remote terminal units) or pump on/off controllers, to talk over a single radio channel in order to bring the data back to pcVue SCADA. CTH Systems supported CNRL with implementing automatic and remote readings of gas compositions from the well, the upload of the corrected gas compositions to each well, and the elimination of variances between the well meter and the IMSCADA™ database. “We couldn’t be happier with how robust and effective the IM-SCADA driver works for us. It helps maximize operational efficiency,” said Jackson. It minimizes the need to physically go to the well sites to download or upload the gas compositions.
Having 178 host servers along with 600 remote clients, CNRL is monitoring about 5,000 – 6,000 data points per host. Of these there are eight pcVue stations that are supervising anywhere from 50-400 wells and one to three facilities per host, depending on location or region. “This translates to thousands of tags and alarm parameters that are being monitored and acknowledged daily,” said Jackson. As the oil flows out of the well, it passes through a pipe arrangement, which is connected to flow lines that bring the oil and gas to gathering stations where sediment, gas, salt water and oil are separated. pcVue is also monitoring the gathering stations.
The pcVue SCADA collects such I/Os from PLCs and RTUS used in production fields and gathering stations such as gas/oil pressures, (ESD), pump start/stop, remote/local pump control, pump speed, pump run/stop, motor operated valves and motor operated valve shut down, choke setpoints/positions,temperature, emergency shutdown and fire alarms etc. “One of the most important factors in our industry is safety. At every stage of the process, pcVue monitors our mission critical operations and maintains all of our safety measures to prevent fires, explosions, and ecological disasters,” said Jackson.
Characterized by remote and widespread operations, CNRL wanted to have each automated activity whether in drilling/production, distribution, transportation or refining supervised from several of its control centers. A solid and securely designed SCADA system must be able to control such critical factors as: flooding, leakage, fire, ESD, oil and gas flow rate and accumulated flow, line pressure, wellhead pressure, pump status, tank level, and gathering station equipment status, among others. Due to the nature of the product, which must be transported from the well to final consumer, and the potential adverse environmental effects of oil/petroleum accidents, SCADA systems are a necessity. “We wanted to leverage SCADA features and benefits that give us the ability to reliably gather more data and achieve more control,” said Jackson.
CNRL is looking forward to reaping the benefits of upgrading its automation systems and is really happy thus far with how well it has been working optimize their processes. “From the first FactoryLink conversion to pcVue, it has been about eight months now that pcVue has been up and running. We are really glad we chose pcVue and IM-SCADA for our SCADA solution and that the configuration process has been very straightforward to implement, especially in consideration that most of our applications are mission critical and work around the clock,” said Jackson.
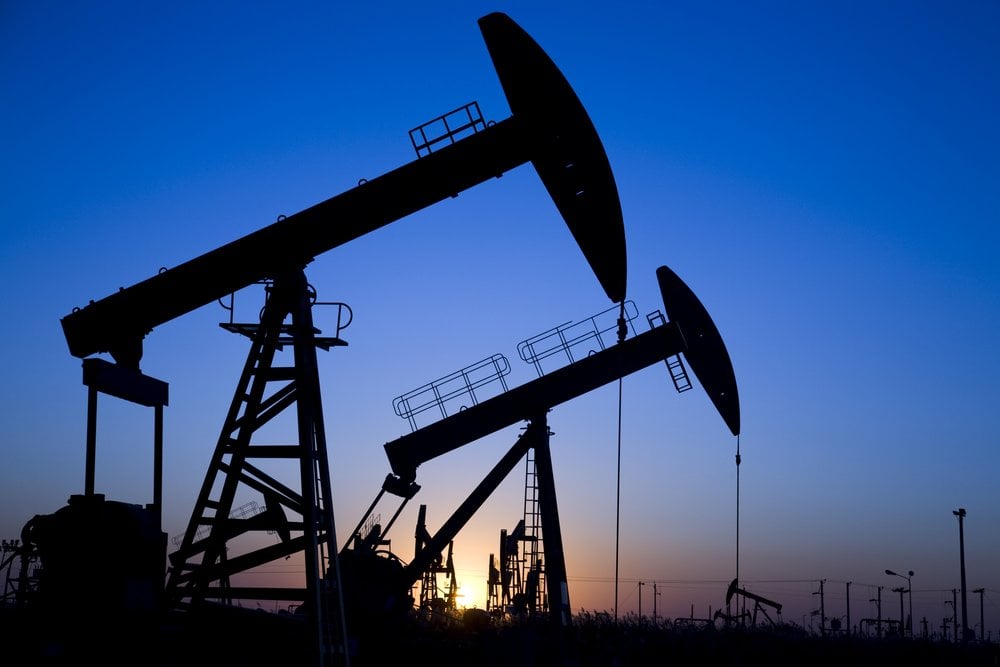
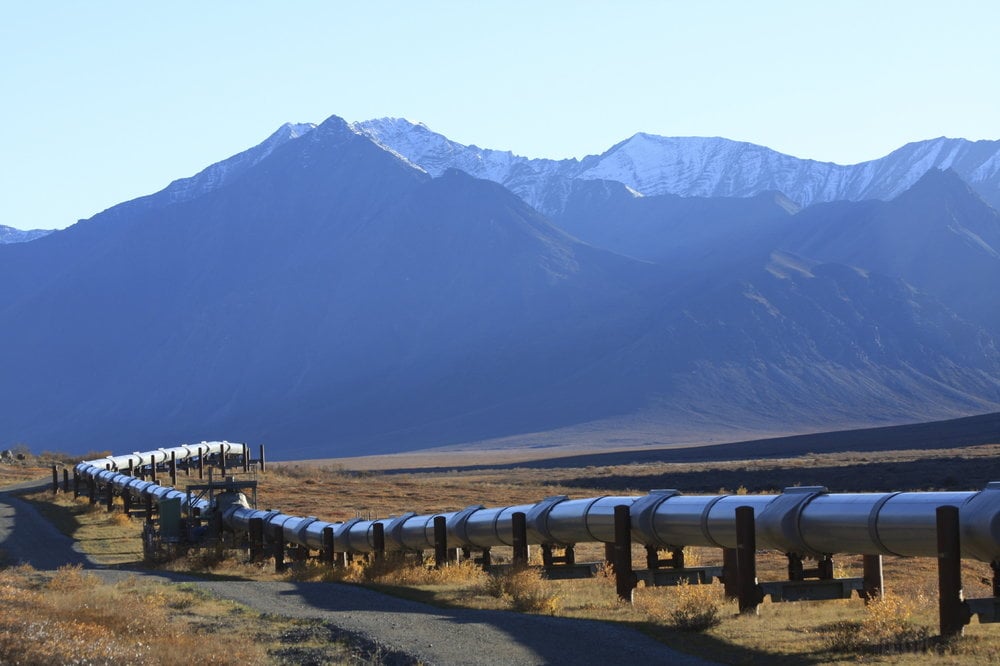