www.industrymiddleeast.com
12
'12
Written on Modified on
Latest Tooling and Surfacing Technology Advance Ganassi and Kennametal Partnership for Indy Cars
Change and Different Thinking Support Winning Record
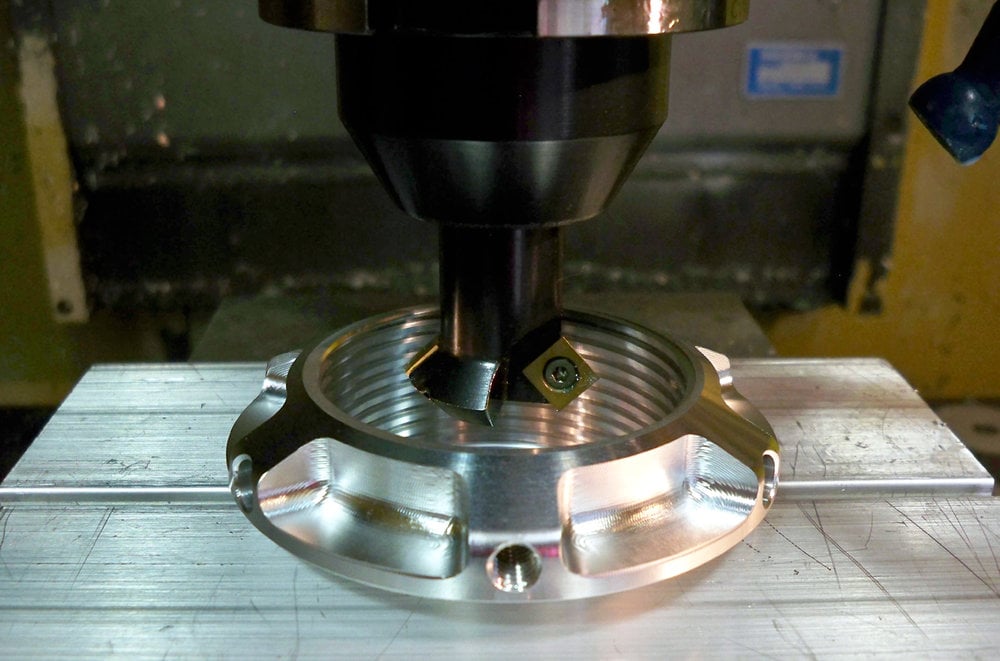
In the wake of Dario Franchitti and Scott Dixon’s dramatic first and second-place finish at the 2012 Indianapolis 500, Chip Ganassi Racing Teams (CGRT) announced a multi-year renewal of its machining technology partnership with tooling and engineering services leader Kennametal Inc.
“We’ve been in business for 23 years and for 19-plus of those, Kennametal has been a partner,” said Chip Ganassi, owner of Chip Ganassi Racing Teams. “We are a 100-percent Kennametal-tooled shop and their logo is on every one of our cars across all our teams and series. But what really makes the partnership even more valuable to the race team is how their expertise helps us perform, even on race day. They come to us with many solutions for different mechanical challenges we face. It is great when you have a partner that can do that.”
Right People, Right Equipment, Right Tools
Tour the Target Ganassi machine shop in Indianapolis and you’ll find a concentrated hive of activity consisting in part of four CNC machines (two multi-axis machining centers and two CNC turning centers, one with live tooling and a sub-spindle). “Ninety-nine percent of our necessary machine work is done right here in-house,” says John Huffman, machine shop supervisor in his 14th season with the team. He points out a steel tripod cover formerly purchased as a factory part now made in house out of titanium for extra strength at reduced weight. “Because of our tooling and machines, it’s actually cheaper to make titanium parts in house than to purchase ready-made steel components,” he says. High-tolerance parts, too, down to 0.0002” on average.
The nature of part production at the Ganassi Indy shop is low-volume, requiring high variety and tight time constraints, or “different parts in a hurry,” as Huffman puts it. His team readily points to the various Kennametal tools providing process advantages, such as PCB tooling for hard turning, resulting in high-tolerance finishes that eliminate the need for grinding, or new five-flute HARVI II™ solid-carbide end mills for roughing and finishing titanium. “Our engineers are confident in specifying more intricate parts with high tolerances and surface finishes because they know we can meet the numbers in-house,” Huffman says.
Kennametal has expanded its 19-year partnership by providing Ganassi’s Indy machine shop with proprietary Precision Surface Management Technology by Kennametal Extrude Hone. Finishing processes like abrasive-flow machining (AFM) have evolved from pure deburring functions to polishing and radiusing within very close tolerances. Add new developments in machine controls, abrasive media, and flow targeting, and the results continue to get much more precise.
Critical Needs
Machined holes, including intersecting holes, in many high-performance applications require surface improvement, usually a lot of polishing to achieve required tolerances. Any smeared metal or micro-cracks at the surfaces created in conventional or non-conventional machining processes increase the risk for diminished performance or failure. To eliminate that risk, engineers factor AFM surface finishes into many component designs, especially where laminar flow, boundary layer turbulence, compressive residual stresses and edge conditioning are important factors. Even in inaccessible areas, surface-finish improvements from an original 120µ inch to 16µ inch or better are possible.
AFM machines can be operated as standalone stations or integrated into production systems. Typically, a part is fixed between two opposed media cylinders, and the machine extrudes abrasive media from one cylinder to the other. The tooling works together with the abrasive media and characteristics of size and viscosity to perform the finite honing of the part. When the media is forced through a restricted passage, its viscosity rise and that holds the abrasive material in place. The media abrades only in this restricted state, so once it exits the restrictive passage, viscosity returns to normal and abrasion is suspended to protect threads and seal surfaces.
Further research and development in AFM at Extrude Hone has resulted in MicroFlow AFM™, where lower-viscosity media and smaller abrasive particle size allows finishing and edge radiusing of holes down to 50 μinches. Fuel-spray nozzles in fuel injectors, for example, can have defined edge radiuses that diffuse fuel microspray for better engine performance.
Huffman adds that because titanium represents a growing portion of his shop’s work, in addition to aluminums and alloy steels, he gleans a number of performance-enhancing ideas from Kennametal’s aerospace-focused “Innovations” catalog, from complex 3D shapes to solutions for deep-hole drills that can reach up to 30 X D. “Our capacity to produce parts in-house will only continue to grow because of this ability to hold tighter tolerances on part dimensions and surface finishes.”
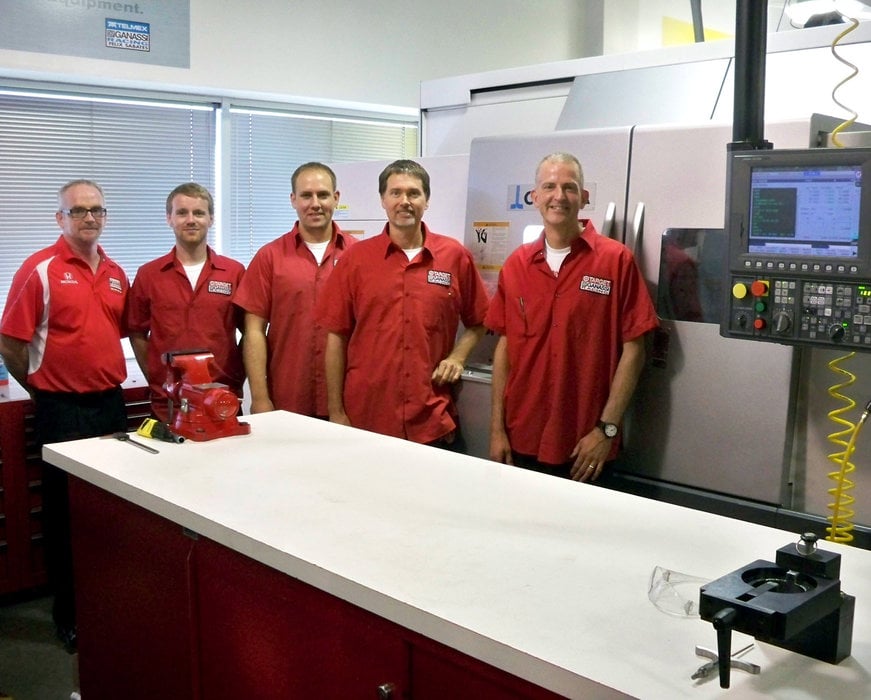
From left to right: John Huffman- machine shop manager, machinists, Curt Saunders, Zack Robertson, Scott Stukenborg, and Jay Marshall.
Caption: Ganassi team member Alphonse Girard loading the Kennametal Extrude Hone machine.
Caption: A full-size Indy car and numerous first-place trophies greet visitors to the Target Chip Ganassi Racing Indianapolis shop.
Caption: The Target Chip Ganassi Racing assembly area is a hive of activity for multiple Indy racing teams.
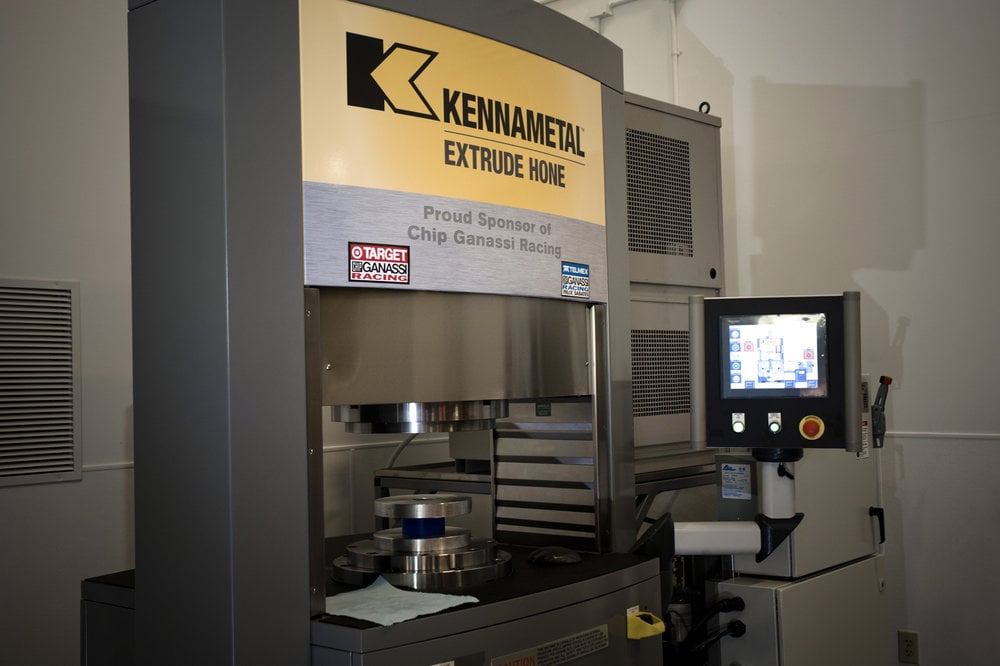
Caption: Advanced surfacing technology poses an opportunity to improve performance on many Indy car components.
Caption: Advanced surfacing technology poses an opportunity to improve performance on many Indy car components.