www.industrymiddleeast.com
24
'13
Written on Modified on
Supporting very high speeds on ballasted track
Vossloh is supplying turnouts and fastenings for use on the Tours – Bordeaux high speed line in France, where ballasted track is being designed to support line speeds in excess of 300 km/h.
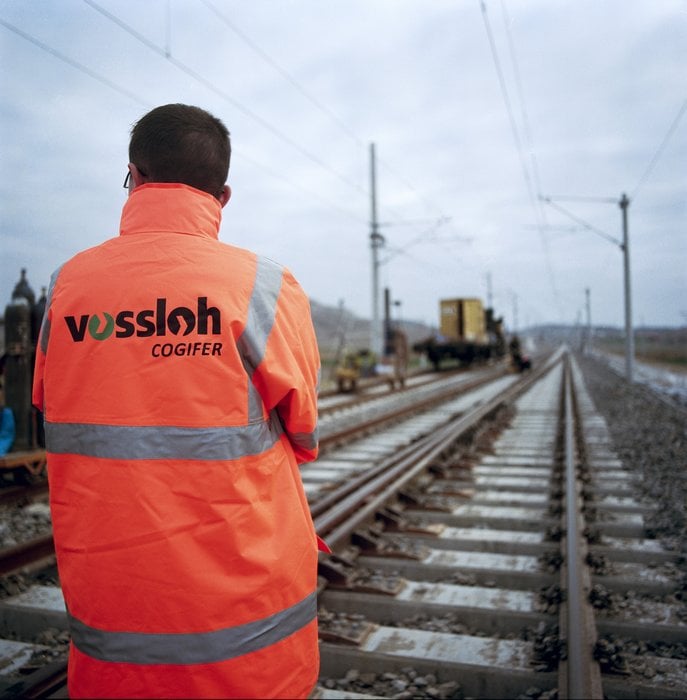
Mohammed Maatallaoui, Sales Director, Region Africa and France, Vossloh Fastening Systems GmbH
Over recent years a slow but steady trend has emerged towards the deployment of slab track on high speed and dedicated fast passenger lines around the world. But there is still no consensus in many markets, and new lines have opened in Spain, Japan and Turkey using ballasted trackforms.
Indeed, across the industry, research and development continues to ensure that track components, materials and assemblies are able to meet the demands of higher traffic loads on lines designed for higher operating speeds. Vossloh Rail Infrastructure, through its Vossloh Cogifer and Vossloh Fastenings business units, is no different, and we are currently producing components for two high speed lines now under construction in France and Morocco.
Costed at €7,8bn of which €6,2bn covers infrastructure, the LGV Sud-Europe-Atlantique project is a public-private partnership to extend RFF’s existing Paris – Tours line southwest to Bordeaux. As well as the 302 km trunk route, the project also covers a further 38 km route-km of connecting spurs to and from the conventional network, requiring no less than 17 junctions to ensure that significant population centres such as Poitiers and Angoulême can still be served. The Lisea consortium which is managing construction expects to build around 400 structures along the alignment, including 19 viaducts and seven cut-and-cover tunnels.
With a design speed of 360 km/h and operating speed of 320 km/h, LGV-SEA should reduce journey times between Paris and Bordeaux by around 50 min to 2 h 5 min when it opens in 2017. Annual ridership is estimated at 20 million passenger-journeys; planners hope that a significant increase in TER regional and long-distance freight services will be possible along the existing corridor, which already enjoys line speeds of up to 225 km/h.
Turnout design
Under the terms of the 50-year public-private partnership, the Lisea consortium led by Vinci Concessions will build and then manage the rail infrastructure. Lisea has in turn contracted out construction work to the Cosea joint venture of Vinci Constructions, Eurovia, BEC, NGE, TSO, Ineo, Inexia, Arcadis and Egis Rail. Once commissioned, the line would be managed by the Mesea consortium of Vinci (70%) and Inexia (30%).
In September 2012, TSO and Vossloh Cogifer signed a contract for the supply of pre-assembled turnouts for LGV-SEA and related servicing and maintenance yards. Tracklaying specialists TSO and its partner ETF are supervising all aspects of track design, fit-out and commissioning, including the sourcing of the rails, turnouts, concrete sleepers, and fastening systems.
Vossloh Cogifer is scheduled to deliver on a ‘just-in-time’ basis more than 200 turnout assemblies between October 2014 and November 2015. The order covers high speed turnouts, sliding rail expansion joints, and conventional turnouts; these are to be produced at Vossloh Cogifer’s plants at Reichshoffen and Fère-en-Tardenois. The scope of supply also includes engineering services, a workshop for pre-assembly by turnout variant, storage and logistics, and the provision of technical assistance for installation at each site.
Vossloh Cogifer has delivered more than 1 700 turnouts for use on lines where speeds exceed 300 km/h. These include more than 200 examples of the 1:65, one of the longest turnout assemblies on the market, where the diverging routes can be taken at speeds up to 230 km/h. High speed switches pose special challenges of reliability, durability and quality. Due to their exceptional length, the blades must be actuated simultaneously at a number of locations along the assembly to ensure smooth movement. Vossloh Cogifer is using a single point machine system able to drive up to 60-m-long movable blades. The blade position also has to be measured very precisely.
All the turnout’s principal components, such as the MCEM91 point motor, Verrou Carter Coussinet clamp lock, Paulvé switch rail location detector and VPM direct locking system, are service-proven and compatible with assorted signalling and train control systems. These also allow a ‘plug and play’ installation alongside Vossloh’s switch and signal control equipment, which minimises interface and commissioning risks.
The turnouts being supplied for LGV-SEA have been designed to carry axle loads up to 22,5 tonnes; the longest switch has a geometry of 1:65 and permits diverging trains to pass at up to 230 km/h. The assembly is powered by a single 600 daN electro-mechanical motor.
The VCC switch-locking mechanism rests on a turnout bearer, and is connected to the switch blade and stock rail. It secures the switch blades in both closed and open positions. The detectors monitoring the blade’s opening and closing/locking phases are mounted on the frame of the locking mechanism.
The VCC switch-locking and VPM movable point-locking can also be fitted with an electric heater. The locking system allows for temperature-derived expansion and contraction of ±55 mm. At all stages, development work complied with the EN 50126 standard as well as strict climatic tests.
The integrated connecting rods move in a recess in the concrete bearer, which allows ease of access to the track bed around the switch for tamping and automated ballast refilling. A cover protects against dust and moisture ingress, while power is supplied to each single drive at 380 V AC. Separate control systems manage the switch and crossing components, and each has its own connection to the interlocking.
Fastenings for ballasted track
In addition to supplying turnouts, Vossloh Fastening Systems is to equip LGV-SEA with 1,1 million pairs of fastening assemblies, delivery of which has already started. Vossloh is to provide its W 14 KIS screw-anchor elastic fastening to meet the specific demands of 320 km/h operation on ballasted track.
The W 14 is a robust, low-maintenance design consisting of five components: two rail tension clamps, an elastic rail pad, and two angled guide plates. These are secured using two sleeper screws driven into plastic insert dowels which are anchored in the concrete sleeper. All fastening components can be pre-assembled manually or by automated machining at the sleeper factory, which enables rapid mechanised installation at the work site.
The fastening design has already been approved by SNCF for use on routes with a line speed of up to 350 km/h, and we expect significant whole-life cost efficiencies in maintenance as replacement of the sleeper is not required when the fastenings are renewed. The fastenings are electrically isolated, and no additional insulating components are required between the clamping element and the rail base. To suit operation with coded track circuits, the W 14 KIS offers an electrical resistance of 20 kΩ. This is greater than that of the W 14 as supplied for many conventional lines, and exceeds the 15 kΩ required by the track design standards.
Adjustments to the vertical and horizontal alignment of the fastening can be undertaken to reflect changes in the track geometry; levelling plates can also be inserted to protect against the effects of frost damage. A geometric adjustment of ±10 mm in increments of 2,5 mm is offered as standard. Continuous welding of the rails can be undertaken by loosening the sleeper screws rather than dismantling the whole fastening.
Ballasted track in Morocco
The development of ballasted trackforms for operation at speeds in excess of 300 km/h is not restricted to France; however, as the French-backed project to build a high speed line between the Moroccan cities of Tanger, Kénitra and Casablanca will also adopt this method. Vossloh Rail Infrastructure has again been contracted to undertake tracklaying and fit-out for the first phase of this 320 km/h line, which covers the 200 km between Tanger and Kénitra.
In June 2012, Vossloh Cogifer signed the contract to supply 148 conventional turnouts, 30 high speed assemblies equipped with swing-nose crossings and 24 sliding rail expansion joints with fastenings; these will be supplied by mid-2014. Between 2013 and 2015, 700 000 sets of fastening systems will be delivered by Vossloh Fastening Systems.
