www.industrymiddleeast.com
21
'13
Written on Modified on
NOV AND SIFCO ASC PARTNER FOR SUCCESSFUL COMPLETION OF UNSCHEDULED REPAIR
SIFCO Applied Surface Concepts (ASC), the world leading supplier of selective plating technology and solutions, worked together with the world leader in oilfield products and services, National Oilwell Varco (NOV) to repair critical damage caused by lightning strike on the Ensco 8505 drilling rig in the Gulf of Mexico within 24 hours of arrival on site, preventing costly unplanned downtime.
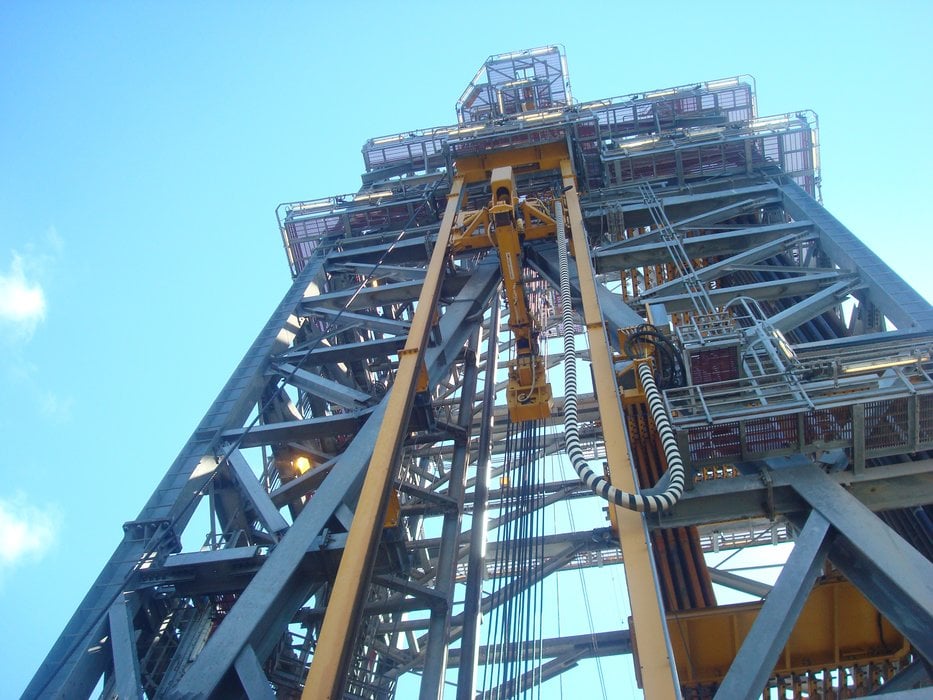
Significant damage was caused to the crown mounted compensator (CMC) cylinder when lightning struck the rig. The CMC is a device used to apply a constant tension to the drill string and compensate for any rig movement. The impact of the lightning strike caused a substantial gouge, the size of a coin, on the CMC cylinder. Without immediate repairs the damage would cause the cylinder seals to leak, resulting in hydraulic fluid loss and the threat of significant lost production.
The Ensco 8505 is one of many oil rigs in the Gulf of Mexico and the sixth of seven rigs in the ENSCO 8500 Series®. In the second quarter of 2011, these rigs had virtually no downtime and achieved 99 percent utilisation as well as being ranked number one in overall customer satisfaction in deep-water drilling by EnergyPoint , an independent survey firm. The company therefore required a speedy solution which would maintain its high operational standards within the industry.
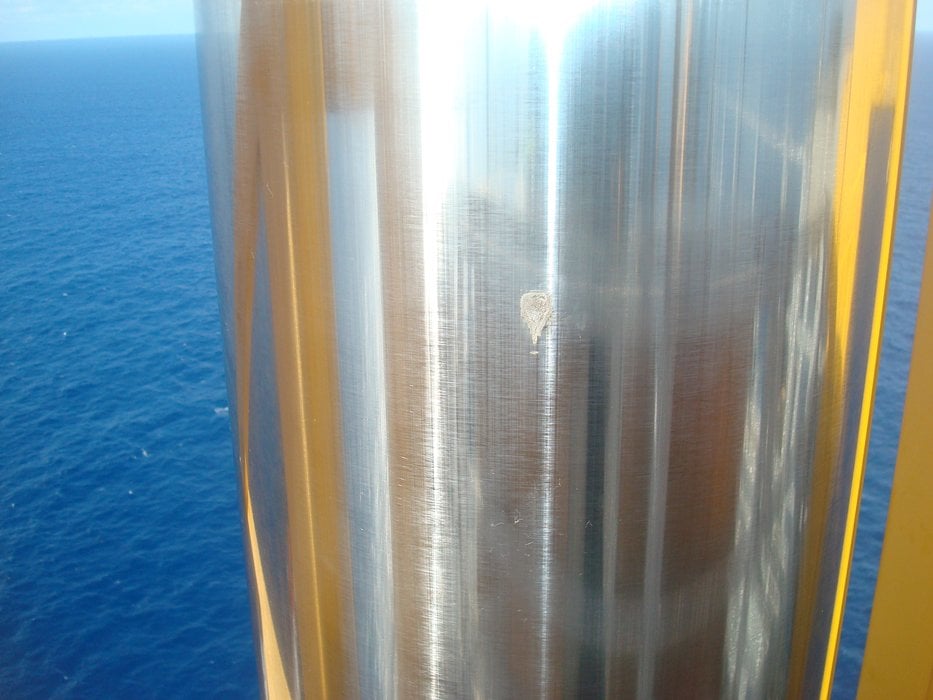
To remove the damaged CMC cylinder from the platform and replace it would be extremely costly, and result in significant downtime, with every hour costing the platform operator thousands of dollars in lost production. NOV and SIFCO ASC came together to solve this problem.
A distinctive solution
The solution was found in SIFCO ASC’s plating process, using SIFCO’s AeroNikl® 7280 for corrosion protection, and Cobalt 2043 to cap the repair for hardness to protect against surface wear. The SIFCO Process® is unique to the company and involves a portable method of electroplating localised areas without the use of an immersion tank. The SIFCO Process® is highly regarded in the oil and gas industry and used on many OEM and repair applications, particularly as components can be plated in-situ and on-site, which ultimately saves time in maintenance, repairs and unplanned downtime.
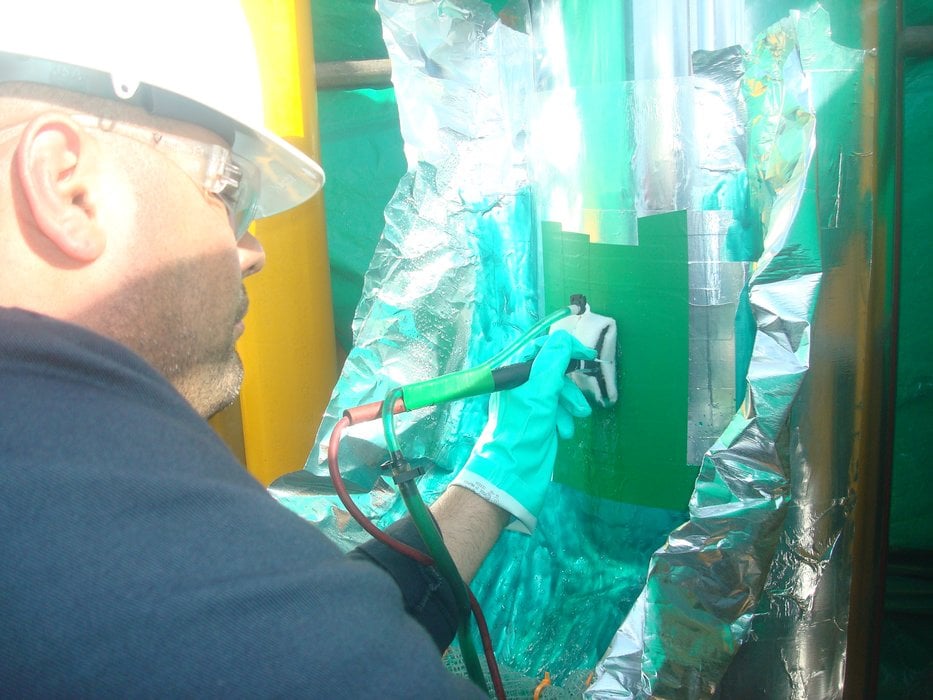
When undertaking the repair work, two SIFCO ASC technicians were situated near the top of the derrick, 450ft in the air, to perform the repair. It took them a total of 24 hours to complete the work and return the platform to full operation, as opposed to three months to replace the shaft.
Jimmy Clark, structural service manager from NOV said: “When rigs are down it can be costly which is why it was important that we sourced a solution that could be completed in as little time as possible, producing outstanding results that would keep the CMC cylinder protected from further damage.”
SIFCO ASC’s experienced, skilled and qualified workforce applies all deposits in strict adherence to the specifications and quality assurance requirements demanded by its customers. They inspect and ensure that their work complies with industry standards as insisted by customers in the oil and gas sector. The SIFCO ASC technicians on this project hold annual certifications to work on oil platforms, which allows for their speedy deployment to site.
Five times the result
The final result was extremely successful. The repaired cylinder was dimensionally accurate to .001” tolerance as compared to the .005” tolerance originally requested by NOV.
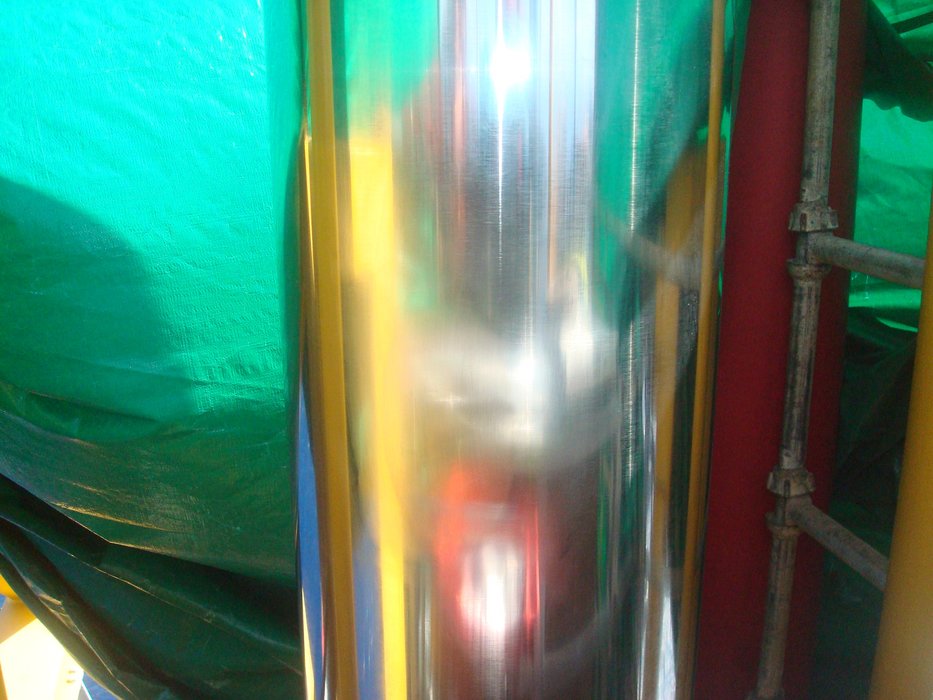
This section of the CMC cylinder will be better protected from corrosion and, in offshore oilfields, metal structures and components are under constant attack from a variety of sources. Although corrosion will initially be uniform across the surface area of the metal, in time it will accelerate into any small crevices. Without SIFCO ASC’s AeroNikl® 7280 this could have ultimately progressed into cracks in the metal, which could have been accelerated by tensile stress, resulting in stress corrosion. According to the “United States Cost of Corrosion Study”, produced by NACE International, one of the world’s leading authorities on corrosion engineering and control, corrosion costs the US oil and gas exploration and production industry $1.4 billion a year.
Similar projects include the repair of the Hydraulic Balance Cylinder on the Transocean Development Driller 1. SIFCO ASC is prepared to help the industry mitigate the threat of corrosion and meet the key challenges of extending equipment life while reducing downtime and reducing operating costs.
Lee Shelton, Managing Director, SIFCO ASC said: “When production halts due to the damage of critical components that are not easily repaired, time is of the essence to reduce the shutdown period to a minimum. Our aim was to restore confidence in the performance and reliability of Ensco 8505’s process operations, and I’m delighted the SIFCO Process® has had a positive impact on its operational performance and profitability.”
NOV provides comprehensive drilling solutions that include technically advanced, field-proven equipment integrated into systems that increase drilling efficiency, enhance Health, Safety, and Environmental (HSE) programs, and maximizes customers’ life cycle economics. It has an ability to design, manufacture, install, commission, and provide aftermarket service for a wide variety of drilling systems and equipment. It has worked with SIFCO ASC since 2009 which has over 50 years’ experience serving the oil and gas market globally, providing a complete range of selective plating solutions combined with industry leading technical support and application advice.