www.industrymiddleeast.com
15
'14
Written on Modified on
NORD Strengthens Partnership with Indian Steel Industry
German Drive Manufacturer established No.1 leadership position in 2013
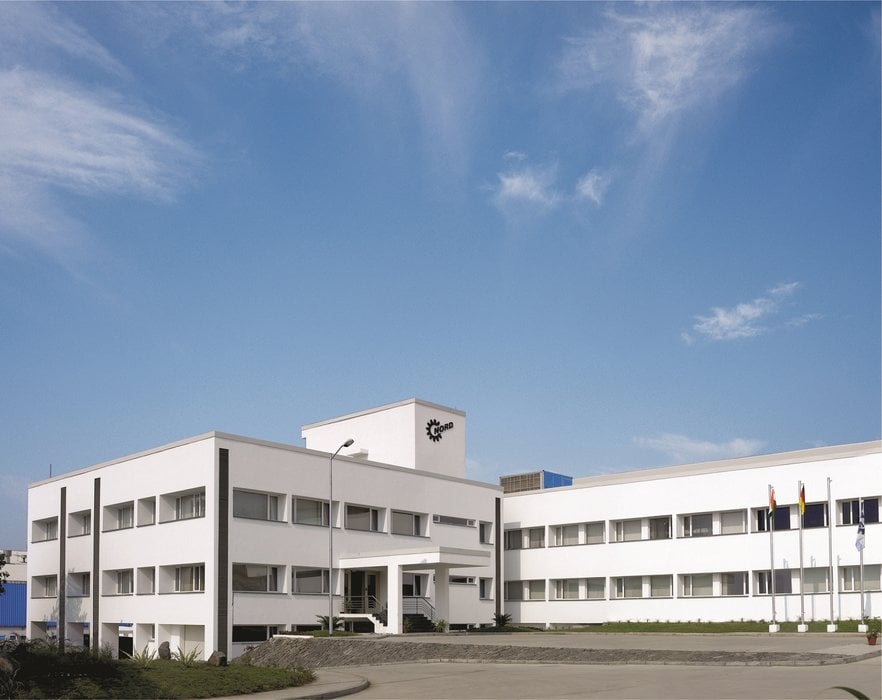
About one out of every two geared motors newly commissioned by the Indian steel industry in the last year has come from the Indian operation of German drive technology leader NORD DRIVESYSTEMS. NORD has become the major mover in the steel & metals sector, peaking at a record 46% of the total drive sales volume in this segment in 2013. In less than ten years of activity in the Indian steel industry, the NORD brand has managed to rise to its commanding No. 1 position on the strength of product quality, reliability and advanced technical know-how. NORD has now supplied several thousand geared motor units to dozens of OEMs as well as all major plant builders and operators in the business across India. Some notable projects include e.g. over 2,000 geared motors for the universal rail mill in the Bhilai Steel Plant; over 1,000 geared motors for steel production, for the heavy plate rolling mill, and for the medium and light structural mill at Jindal Steel & Power; over 500 drive units for the section mill at Jayeswal NECO Raipur, and over 200 units for EOT cranes, transfer cars, and casters in TATA KPO.
As geared motors are exposed to heavy mechanical and thermal stress, they must nonetheless provide for trouble-free operation in continuous processes, preferably with zero maintenance, all the while achieving an advanced level of efficiency. Offering a versatile range of geared motor types to choose from, NORD can draw on five decades of experience in the steel & metals sector. Industry specialists can provide advice regarding parameters like power/torque requirements, bearing life, and oil temperature in order to enable users to select the most suitable product for a specific steel mill application – from a single system to several thousand units. NORD India has committed a highly qualified and efficient team of experts to a special sector management cell that focuses exclusively on the iron and steel segment. Comprehensive NORD drive solutions are available for various different areas of the metals processing industry, including applications in coke and iron making, continuous casting, rolling mills, shearing lines (lengthwise and crosswise), cooling beds, ladle transportation, furnace charging and discharging, roller tables in section mills, plate mills, hot and cold rolling mills etc.; and various other conveying applications all across production processes. An extensive range of industrial gears, parallel shaft gears, helical inline gears, helical bevel gears, and helical worm gears with solid or hollow shafts can be combined with highly robust cast iron motors, e.g. ring fin types, as well as with smart decentralized drives that are suitable for applications throughout the industry.
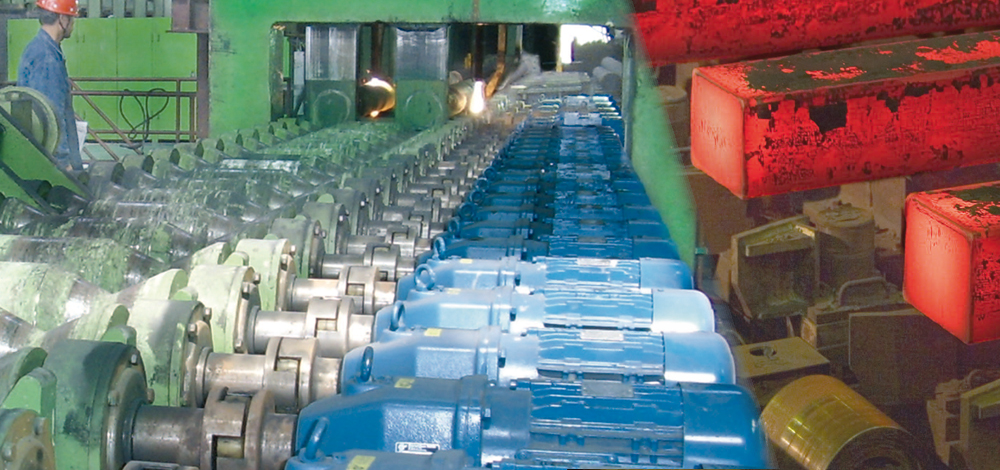
Roller table drives are a case in point for highly available, heavy-duty systems featuring superior resilience – they must withstand a harsh environment with high ambient temperatures, heavy shocks and vibrations and heavy loads, and have to provide stalling capability. Gears in these applications require an especially robust housing material that accomplishes vibration absorption, typically, EN-GJL-200 (GG20) or EN-GJS-400-15 (GGG40). Configuration options include reinforced shafts e.g. made from 42CrMo4, special coatings, synthetic lubricants, and special Labyrinth seal designs. Roller table motors must deliver high starting and breaking torques, run at variable speeds, and be capable of instantly reversing direction. Frequent acceleration and deceleration is the rule; operating modes in these applications vary greatly, with S1, S5, and S9 duty most frequently required. Every roller table motor’s load torque must be high enough to reliably handle overload, i.e. cover for a neighboring drive system in case that unit should fail. These motors will usually be either ring-fin or straight-fin totally enclosed non-ventilated (TENV) types, which NORD manufactures from high-strength cast iron that ensures maximum shock resistance. Featuring a larger amount of material as well as larger bearings and shafts, these systems withstand greater loads and have a longer service life than conventional industrial motors in the same performance range. However, NORD also provides alternative motor solutions featuring various modes of ventilation. Ancillary components such as brakes or incremental or absolute encoders can be supplied as well.
While most areas in steel plants are hot and dry, with temperatures reaching 60 °C or more, there are also some like descalers, rolling stands, and sections such as cooling lines where conveyor drives must additionally provide IP66 ingress protection against spray water. Steam can pose a considerable corrosion threat as well. ISO F insulation will suffice for drives in many cases, but class H motors must also be available on request to address particularly demanding conditions. NORD’s extensive range of dedicated drive products and proven metals sector know-how ensure that steel industry OEMs, EPC contractors and end users always have the full range of options at their disposal.
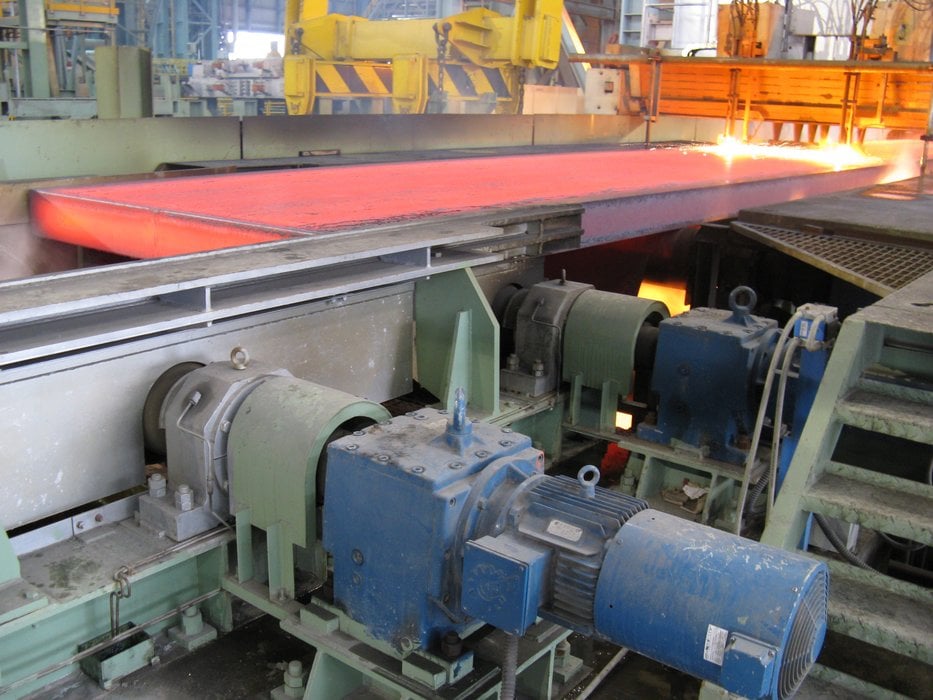
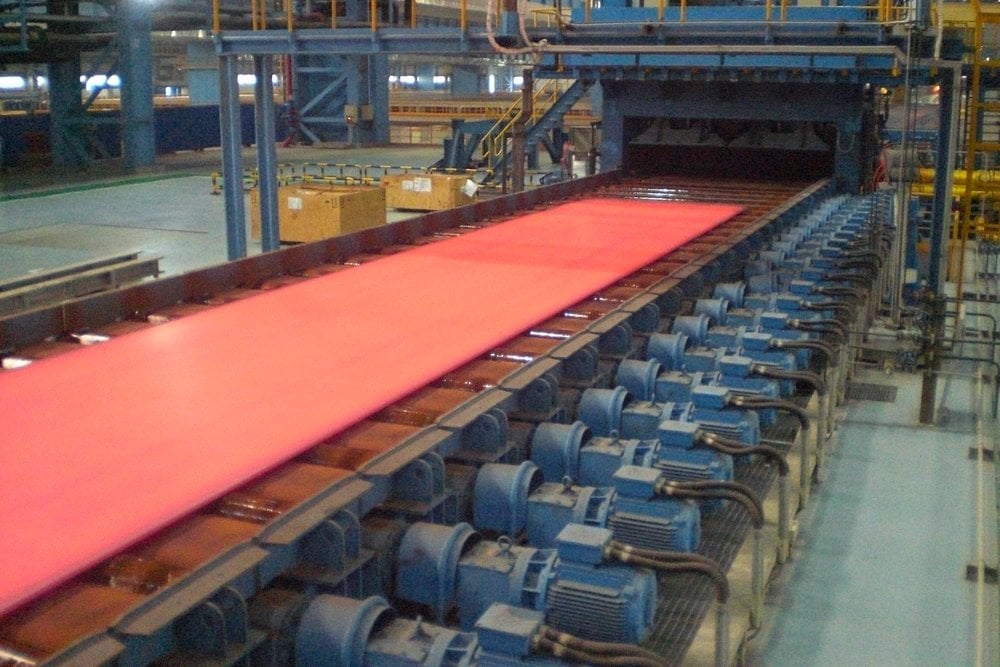