www.industrymiddleeast.com
18
'14
Written on Modified on
Loiselet Foundry at Dreux relocates production to France in new, highly automated facilities equipped with Verlinde powered hoists.
LOISELET Foundry, whose specialty is the production of cast iron products, is situated at Dreux, 70 km west of Paris. Founded by César Loiselet in 1850, the company is still owned by the family. The fifth generation, currently represented by Sylvain Loiselet, Chairman and Managing Director of the company and Sébastien Loiselet, is still very much at the helm. It will soon be the turn of sixth generation children to integrate the company, little by little, in various capacities.
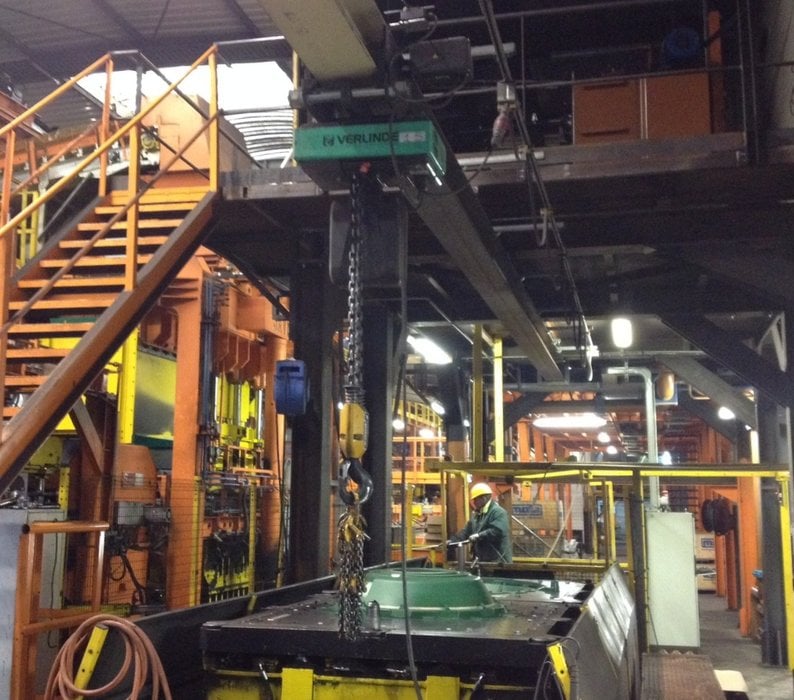
To ensure ongoing economic performance, production was relocated in 2001 to a factory in China. In 2011, as conditions for the relocation of production to France became favourable, the building of production facilities got under way at Dreux.
The return to Dreux offered numerous advantages in terms of product quality, proactive project management, logistics, delivery dates and carriage costs. Indeed, LOISELET's main markets are to be found in Europe and North America (USA and Canada).
2012 was a landmark year with the opening at Dreux of highly automated production facilities in an 8,000 m² plant. The payroll of ninety-two includes an engineering team of six and a production workforce of sixty. From the outset, two steel melting furnaces were built to work in tandem offering a foundry capacity of twelve metric tons an hour. The factory's increase in output is set to be rapid. It is planned that the €12m turnover posted in 2013 will increase to €35m when production is at its peak in approximately three years time. It is probable that the Chinese facility will be closed down at that time.
Handling of heavy items.
As the weight of items to be handled is between 20 and 400 kg, handling equipment is indispensable. Thus it was that when the factory was designed, powered hoists, considered to be vital to the production chain, were built into the project. Preference was given to VERLINDE's EUROSYSTEM ST equipment associated with Eurochain VL electric hoists that are fitted with electrical handheld controls for UP/DOWN travel while horizontal travel is achieved by hand. The in-house engineering department designed the roller path bearing structure in compliance with current standards and the installation was inspected and approved by Coface.
Workshops fitted out with Verlinde hoists
• In the burring workshop, at the foundry exit point, a EUROCHAIN VL hoist serves a workstation allowing parts to travel over a distance of 10 m.
• The machining workshop, dealing with drilling, tapping or dressing of parts, operates with two automatic, five-spindle machines fed by two hoists of the EUROCHAIN VR new generation.
• Some parts require a paint coating operation. The paint line offer two techniques, one by dip coating, the other by spraying. Two hoists are used without indifferently for the two workstations.
• At the shot blasting station where metal shot for cleaning parts is shot at the speed of 80m/s, four Verlinde hoists fitted with electromagnets meet all production requirements.
• Lastly, no parts can be cast without moulds and the metal moulding workshop is a vital cog in the product quality process. The workshop's production capacity is 80 moulds per hour. The EUROCHAIN VR hoist serving this workshop, fitted with an electrical UP/DOWN control, ensures aluminium moulding patterns are delivered to the sand casting mould boxes.
So it is that nine identical VERLINDE hoists move all loads in the LOISELET plant workshops at Dreux. According to Camille Loiselet, Marketing Manager and in charge of supplier relations, VERLINDE was an obvious choice because of convenience of distance of the VERLINDE agency, value for money and reliability of the equipment, while another important criterion was facility of maintenance and breakdown clearance due to uniformity of the hoist fleet.
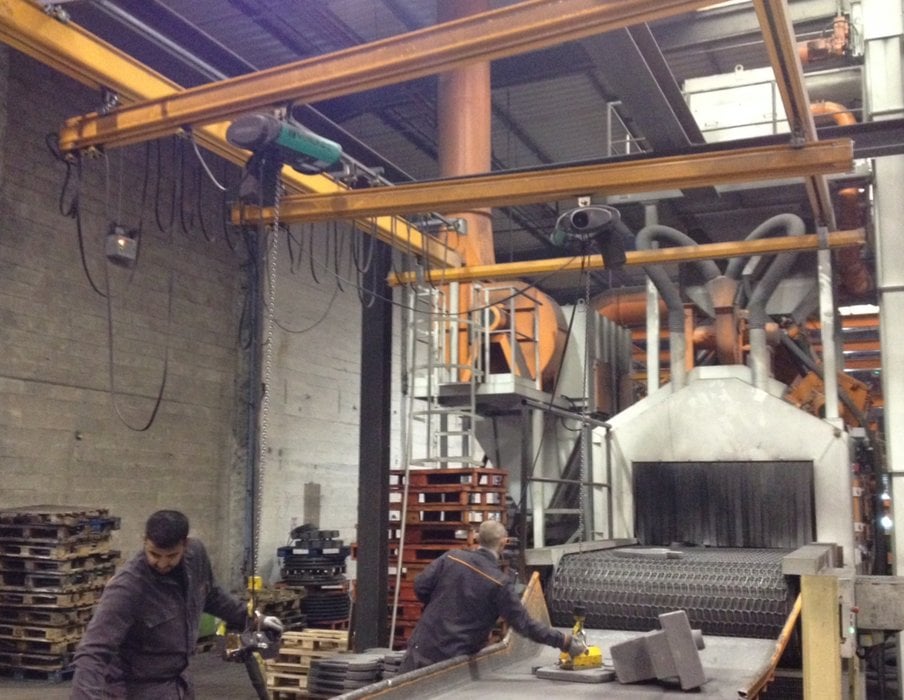
Wide variety of products
LOISELET Foundry manufactures products in gray cast iron (flake graphite) and spheroidal graphite for various markets:
Industry (85% of turnover) which embraces farm machinery, rail industry, building industry and civil engineering. Road construction (10% of turnover) represents a wide variety of products such as manhole covers, inspection holes, gully holes, etc. Lastly, the art foundry and street furniture market account for 5 % of turnover: manufacture of street lamps, chimney plates, grill plates, park benches, fountains, garden boxes, etc.